A noi di Taylor Guitars piace dire che la sostenibilità è un percorso, non una destinazione. È una mentalità che ci spinge sempre a migliorare. Proprio per questo motivo stiamo studiando nuovi modi per lavorare con maggiore responsabilità senza compromettere gli standard sui quali è fondata la nostra azienda: oltre al semplice consumo di legno, stiamo analizzando il dispendio energetico, i prodotti plastici e monouso e perfino le nostre magliette. La perfezione è ancora lontana, ma stiamo facendo passi avanti. Dopotutto si tratta di un percorso.
Per essere un’azienda responsabile, non si può lasciare da parte la trasparenza. Perciò in questo articolo mi sono concentrato sulla finitura delle chitarre ripercorrendo il nostro passato, la situazione attuale e la direzione che stiamo cercando di intraprendere.
Comincio col dire che tra gli appassionati di chitarre la finitura può essere una questione che suscita forti emozioni. Fidatevi, se volete accendere un dibattito tra liutai e musicisti, provate a parlare di finiture. Ciò è dovuto in parte alla lunga storia delle finiture per gli strumenti a corde, ma anche alla moltitudine di opinioni sul modo in cui possono influenzare il suono, l’aspetto e la sensazione di una chitarra.
Ben più di un rivestimento
Le chitarre che raggiungono il reparto finiture del nostro impianto a El Cajon, in California, vengono sottoposte a una serie di processi, tra cui sabbiatura, colorazione, riempimento dei pori e applicazione della finitura. Una buona rifinitura non consiste solo di un rivestimento protettivo, ma è un sistema sofisticato che comprende diverse tecnologie e materiali applicati in una successione di livelli integrati che ricoprono funzioni specifiche. Ad esempio, il riempitivo per i pori penetra nel legno, stabilizzandolo, specialmente nel caso dei legni a pori aperti come il mogano. Un’ulteriore passata di vernice protegge il legno fornendo la quantità giusta di smorzamento (per maggiori informazioni su finiture e smorzamento, si veda il box laterale). Un altro strato del sistema di finitura è rappresentato dalla copertura finale, applicata di solito per motivi estetici, che a volte evidenzia le venature del legno e migliora l’uniformità del colore.
La storia dei materiali per finiture
Nel corso dei secoli sono stati usati molti materiali diversi per rifinire gli strumenti musicali in legno: oli (di lino o tung), cere, gommalacca (una resina prodotta dalla cocciniglia della lacca in India e Tailandia), vernici e innumerevoli smalti. Essenzialmente, la maggior parte delle finiture è composta da tre elementi: un solido (come la resina), un legante (per far aderire la finitura al legno e i solidi tra loro) e un veicolo (solventi, oli) che aiuta a sciogliere la resina per renderla più spalmabile.
Per capire meglio l’evoluzione delle finiture per chitarre, comprese le nostre, è necessario ricordare gli strumenti che ne hanno influenzato lo sviluppo, come l’oud e il liuto. Secoli fa, il legno di questi strumenti veniva protetto usando ingredienti naturali disponibili in loco, come ad esempio la colla d’albume, una miscela di zucchero (impiegato come resina per migliorare la durabilità), chiara d’uovo (l’agente legante) e miele (il veicolo per l’applicazione, che forniva anche un certo grado di flessibilità alla superficie). Forse in alcuni casi veniva anche aggiunta linfa indurita, estratta probabilmente dall’acacia.
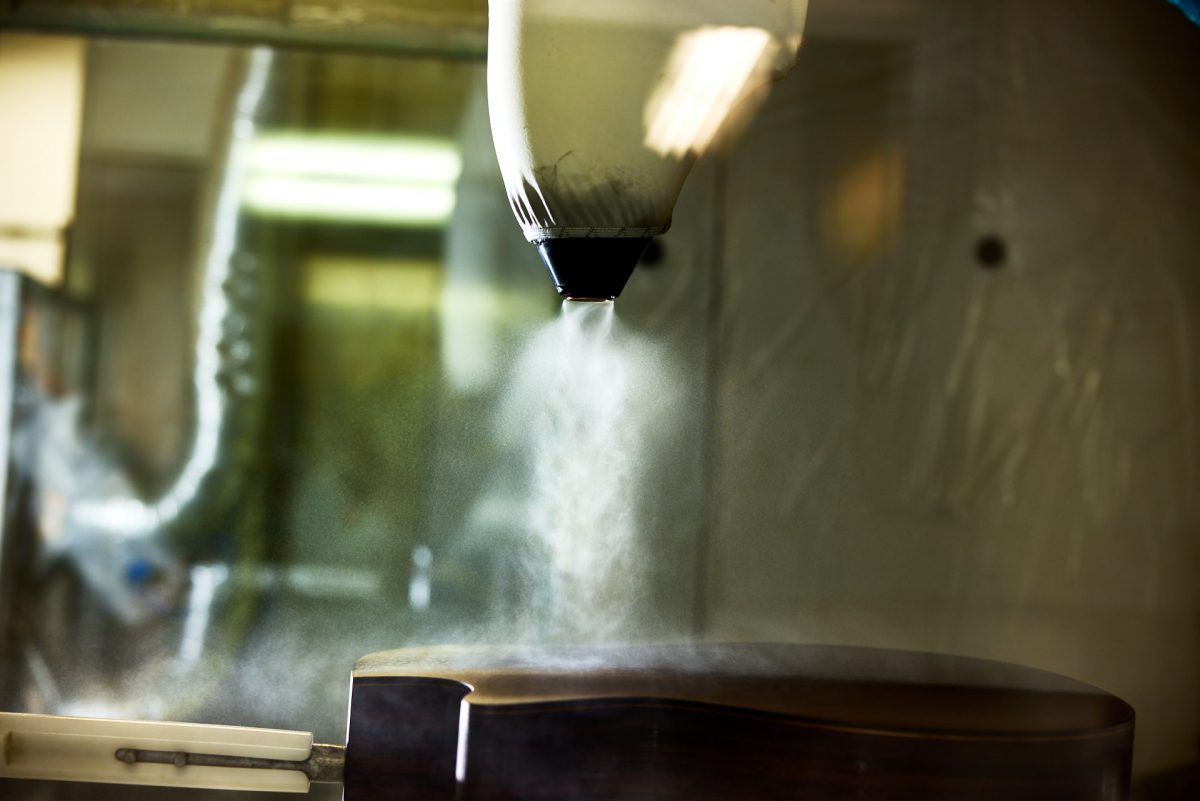
Spessore e smorzamento della finitura
Esiste un nesso preciso tra spessore della finitura e smorzamento. Ad esempio, qui alla Taylor abbiamo trattato questo argomento durante l’introduzione di alcune delle nostre finiture sottili ideate per migliorare il suono. Una finitura troppo pesante limita eccessivamente la risonanza e la musicalità della chitarra. Ma al contempo una finitura troppo leggera (o del tutto assente) non fornisce un controllo sufficiente dello smorzamento, che può provocare un contrasto tra gli armonici e, a volte, un’acustica stridula. Perciò lo smorzamento non è sempre un aspetto negativo della componente sonora.
Finiture francesi
Le finiture degli strumenti in legno maturarono nel 1600, con il violino che fece da apripista per le finiture che seguirono. Una tecnica di finitura lucida nota come “finitura francese” passò dal mondo dei violini a quello delle chitarre classiche e parlor durante il XIX e il XX secolo. Il nome di questa tecnica deriva dal suo uso diffuso nei mobilifici francesi dell’epoca vittoriana: si trattava di un processo di lavorazione molto complesso in cui si applicavano numerosi strati sottili di gommalacca naturale, prodotta dalla cocciniglia della lacca, sciolta in alcol denaturato e strofinata con un panno imbevuto d’olio. Dato che l’alcol evapora in fretta, i tempi di asciugatura tra ogni applicazione sono molto brevi. Tuttavia, poiché ogni rivestimento è sottilissimo, si rendono necessarie centinaia di passate (non sto esagerando) per ottenere la superficie lucidissima che la gente adora.
Laccatura alla nitrocellulosa
Nel 1921 l’azienda chimica Dupont inventò la laccatura alla nitrocellulosa per l’industria automobilistica. Si trattava della prima finitura sintetica moderna: era resistente, si asciugava in pochi minuti e si poteva applicare con una pistola a spruzzo, risultando quindi perfetta per la produzione di massa. Questo processo fu presto adottato dai lavoratori del legno, tra cui i produttori di chitarre.
Ma la laccatura in nitrocellulosa aveva i suoi difetti. Innanzitutto, con i metodi tradizionali di verniciatura a spruzzo, l’efficienza di trasferimento (la quantità di finitura che si lega al prodotto senza disperdersi nell’aria) si aggirava intorno al 10 percento. Per le chitarre di legno, i solventi necessari per la sua applicazione richiedevano fino a due settimane di essicazione. In certi casi i solventi potevano continuare a evaporare per mesi o perfino anni, rendendo la finitura più densa e sottile. Inoltre, col passare del tempo, le finiture in nitrocellulosa tendevano a ingiallirsi e, con notevoli variazioni di temperatura, potevano causare piccole smagliature, note con il nome di finish checking (“finitura a quadretti”). Alcuni collezionisti di chitarre d’epoca ritengono che tali caratteristiche aumentino il fascino dello strumento.
Solventi e COV
Quando la laccatura in nitrocellulosa era ancora una novità, non si conoscevano appieno gli effetti collaterali dei solventi. Infatti, se si applicava con pistole a spruzzo industriali, la nitrocellulosa rilasciava quantità significative di composti organici volatili (COV), molti dei quali pericolosi per la salute e per l’ambiente. Certo, i COV si trovano dappertutto e si possono verificare anche in contesti normali, come quando si stappa una bottiglia di vino. Si tratta solamente di un gas, ma certi gas sono innocui e altri no. I COV emessi usando pistole a spruzzo per applicare la laccatura in nitrocellulosa possono risultare velenosi e provocare effetti nocivi per la salute, tra i quali irritazioni temporanee a gola, naso e occhi, respiro affannoso, mal di testa, nausea, vertigini e problemi alla pelle. A lungo termine questa sostanza può danneggiare polmoni, fegato, reni o il sistema nervoso centrale. Oggigiorno le finiture a laccatura in nitrocellulosa vengono ancora usate in molti settori, tra cui la produzione di chitarre, anche se il loro impiego è molto più sicuro grazie alle misure di protezione per i lavoratori.
L’evoluzione della finitura Taylor
Nel corso degli anni, i progressi scientifici nel mondo della plastica e dei polimeri hanno reso disponibili nuove forme di finiture. Molte di esse, come la conversione della vernice, uretani, poliuretani, poliestere e acrilici, sono state adottate dall’industria delle chitarre. Non sono altro che semplici resine ottenute con metodi scientifici e ognuna di esse emette un certo livello di COV. Quando Taylor Guitars aprì i battenti nel 1974, l’azienda adottò diverse finiture e metodi di applicazione diffusi nel settore a quell’epoca, dalla laccatura in nitrocellulosa alla conversione di vernice e, in seguito, ai poliuretani. Tutti questi materiali erano dannosi per l’ambiente e avevano tempi di indurimento molto lunghi.
Intorno al 1985 la Taylor cessò di impiegare finiture con laccatura in nitrocellulosa. Negli anni seguenti il reparto finiture Taylor continuò a trasformare i nostri metodi, passando da un approccio prevalentemente manuale e laborioso a sofisticate tecniche scientifiche.
La crisi è la madre di ogni invenzione
Bob Taylor è sempre stato un innovatore, ma a volte gli stimoli possono arrivare dall’esterno. Come quando nel 1991 Bob ricevette una lettera dallo Stato della California: fu informato che di lì a poco Taylor Guitars non avrebbe più potuto usare molte delle finiture impiegate nel settore. Gli altri produttori di chitarre avrebbero potuto continuare a utilizzarle, ma non quelli con sede in California. Per un’azienda giovane e in crescita, era un boccone amaro da mandare giù.
Bob vede la luce
Poco tempo dopo, Bob frequentò un seminario sull’uso della luce ultravioletta (UV) per accelerare il processo di indurimento delle finiture. Poi tornò in fabbrica e dichiarò: “Questa è la direzione da seguire. Dobbiamo sviluppare una finitura più ecologica e a UV per le nostre chitarre, costi quel che costi”. Ma c’era un problema. Non esisteva ancora l’indurimento a raggi UV per oggetti tridimensionali come le chitarre, e non si poteva dire che i produttori di finiture stessero sgomitando per aiutare una piccola azienda di un settore poco noto. Perciò assumemmo un chimico che lavorò insieme al responsabile del nostro reparto finiture, Steve Baldwin, per creare un nuovo rivestimento e sviluppare un metodo per ottenere un riempitivo e una copertura trattabili con i raggi UV. Nel frattempo Matt Guzzetta, il nostro progettista di macchinari e strumenti, ideò e realizzò un forno di indurimento fatto su misura per trattare la finitura in 30 secondi, rispetto ai 12 giorni di indurimento ad aria necessari per la laccatura in nitrocellulosa.
La nuova finitura si basava sul poliestere e conteneva meno solventi, riducendo quindi le emissioni nocive. A differenza della laccatura in nitrocellulosa, questa finitura era molto meno propensa a ingiallire col tempo e non insorgevano crepe con le variazioni di temperatura. Nel 1995 l’applicazione di finiture con indurimento a UV venne incorporata nel processo produttivo e la Taylor divenne il primo produttore di chitarre ad adottare le finiture a raggi ultravioletti: queste dimostrarono una maggiore resistenza e qualità acustica grazie al loro minore spessore. Anche l’enorme riduzione dei tempi di essiccazione migliorò l’efficienza produttiva riducendo al contempo le emissioni di COV.
Ritorniamo ai tre componenti di base delle finiture di cui parlavamo prima: un solido, un legante e un solvente (o veicolo). Come ci spiega il progettista di chitarre Andy Powers, la finitura con indurimento a UV rappresentò una rivoluzione perché venne meno il bisogno di usare solventi.
“La finitura a UV è composta solo da un solido e da un legante”, afferma. “I due componenti vengono catalizzati e passano dallo stato liquido a quello solido. Non è necessario un solvente per renderli spalmabili. In altre parole, il solido e il legante si possono stendere fin da subito, per poi cambiare stato quando vengono spalmati sulla superficie grazie alla luce a UV, eliminando gran parte dei solventi necessari. Così facendo non bisogna applicare dieci rivestimenti con un tasso di evaporazione dell’85 percento: ne bastano due in cui la quasi totalità della finitura rimane sull’oggetto, a parte quel poco che viene levigato”.
Una soluzione conveniente per l’azienda, più sicura per i lavoratori e più rispettosa dell’ambiente.
Buffy l’ammazzachitarre e l’attrazione elettrostatica
Il passo successivo della Taylor fu cercare di ridurre lo sforzo fisico del processo manuale di lucidatura e migliorare l’uniformità delle applicazioni. L’introduzione di questa nuova tecnologia fu problematica e i primi tentativi di programmazione di un sistema robotico di lucidatura valsero al macchinario il soprannome di “Buffy l’ammazzachitarre” (dall’inglese to buff, “lucidare”), ma col tempo il team imparò a regolarlo correttamente.
Qualche anno dopo si ricorse nuovamente alla tecnologia robotica, stavolta per la verniciatura a spruzzo: si ottenne una migliore efficienza di trasferimento così da ridurre lo spreco di materiali. L’efficienza di trasferimento venne incrementata ulteriormente con l’impiego dell’attrazione elettrostatica tra finitura e chitarra, in cui si utilizza un atomizzatore rotante e un ambiente climatizzato per ottimizzare l’adesione della finitura. In questo modo l’efficienza di trasferimento passò dal 15 percento della nebulizzazione manuale all’85 percento del metodo robotico/elettrostatico. Anche in questo caso si ridussero i COV e gli sprechi, ottenendo standard più uniformi e un ambiente di lavoro più sicuro.
Ci tengo a precisare che l’impiego di robot non ha comportato alcun taglio di manodopera. Abbiamo semplicemente facilitato un po’ la vita ai nostri lavoratori e limitato l’impatto ambientale dell’azienda.
Il nostro sistema di lucidatura robotica permette una maggiore consistenza eliminando la mole di lavoro fisico richiesta dalla lucidatura a mano.
Sempre più sottili
Nel 2011, l’arrivo di Andy Powers ci portò a sviluppare finiture ancor più sottili (possibili grazie alle tecnologie adottate dalla Taylor). Questa spinta innovativa richiese un processo di produzione ancora più scrupoloso, dal momento che una finitura più sottile riduce il margine di errore in fase di lavorazione. Infatti le nostre finiture non si ottengono aggiungendo strati su strati di vernice, ma sabbiando e levigando fino a raggiungere lo spessore desiderato. Per migliorare la qualità acustica, Andy voleva una finitura più sottile e Chris Carter (il successore di Steve Baldwin) e il suo reparto riuscirono a ridurre lo spessore della finitura lucida da 0,15 mm fino a un minimo di 0,089 mm su alcuni modelli. Per darvi un metro di paragone, un normale foglio di carta è spesso 0,076 mm (siamo in grado di misurare con precisione lo spessore delle finiture con un apparecchio a ultrasuoni).
Finitura ad acqua
Dal 2019 la Taylor ha iniziato a usare una finitura precatalizzata a base d’acqua per alcuni modelli. Questa offre un’ottima adesione, produce meno COV nocivi e, oltre a essere più rispettosa dell’ambiente, secondo molti chitarristi risulta più gradevole al tatto.
L’origine delle finiture ad acqua di Taylor Guitars si deve a un passaggio in auto e a una pandemia globale. Un giorno Bob Taylor stava guidando la sua nuova Tesla con Chris Carter e i due erano intenti ad ammirare il cruscotto in legno: Chris ipotizzò che si trattasse di una finitura ad acqua e promise di informarsi. Poco tempo dopo Chris cominciò a condurre test ed esperimenti su chitarre scartate e di lì a sei mesi trovò una finitura opaca alternativa, più sicura e facile da usare rispetto alla conversione di vernice. Chris lo riferì ad Andy Powers e qualche settimana dopo Andy iniziò a usarla su un prototipo al quale stava lavorando. I test diedero ottimi risultati.
Poi, il 19 marzo 2020, la pandemia di COVID-19 causò la chiusura dello stabilimento, seguita qualche giorno dopo dalla nostra fabbrica a Tecate. Ci dissero di restare a casa, come a tanti altri in tutto il mondo. Poi successe una cosa particolare: la gente iniziò ad annoiarsi. Molte persone ripresero in mano le loro vecchie chitarre e decisero di comprarne una nuova.
La nostra serie American Dream nacque in questo periodo: fu una reazione pragmatica a una filiera produttiva alterata e imprevedibile a causa della pandemia. Per farla breve, dopo aver esaminato il legno a nostra disposizione, Bob e Andy decisero di “ingegnarsi con ciò che avevano” e realizzarono una chitarra pratica in legno massello e catenatura V-Class che fosse prodotta negli Stati Uniti e che si potesse vendere a un prezzo più contenuto. Le chitarre American Dream sono state un grande successo, ma si è parlato poco del notevole passo avanti della Taylor nelle finiture a base d’acqua.
Quando ci permisero di far tornare in fabbrica piccole squadre di lavoratori con le nuove norme di distanziamento sociale, ci ritrovammo sotto pressione. La nostra azienda doveva lottare per sopravvivere e avevamo bisogno di maggiori risultati con meno mezzi. Ci serviva un processo di finitura più snello e veloce, ma Chris e il suo reparto erano già pronti con una nuova finitura ad acqua che avremmo poi usato in diversi modelli American Dream e anche nella nuova chitarra GT Urban Ash. Il successo fu immediato: risultò più resistente rispetto alla conversione della vernice e il processo di applicazione era più rispettoso dell’ambiente.
Ottenere di più per meno
Nello scorso numero di Wood&Steel avevo parlato dell’importanza dell’efficienza nel percorso verso la sostenibilità, nonostante sia spesso sottovalutata. Le continue innovazioni della Taylor nelle finiture per chitarre costituiscono un ottimo esempio di questo uso più intelligente dei materiali: il numero crescente di leggi a difesa dell’ambiente in California ci ha spronato a realizzare una finitura in poliestere indurito a UV più ecologica e sottile; un’iniziativa ideata per ridurre lo sforzo fisico del processo di lucidatura manuale (e per migliorare l’uniformità) ha portato allo sviluppo di robot per la verniciatura e la lucidatura che hanno migliorato l’efficienza di trasferimento; un giro nella Tesla di Bob e una pandemia globale hanno velocizzato l’adozione delle finiture ad acqua. E tutto ciò ha comportato un minore impiego di materiali aumentandone la sicurezza. Un risultato migliore per Taylor Guitars, per i suoi lavoratori, per l’ambiente e per i chitarristi.