Hier bei Taylor Guitars sagen wir gerne, dass Nachhaltigkeit eine Reise ist, kein Ziel. Das ist eine Einstellung, die uns davor bewahrt, selbstgefällig zu werden. Dementsprechend befassen wir uns mit einer Reihe von Themen – über das offensichtliche Thema des Holzverbrauchs hinaus – einschließlich des Energieverbrauchs, der Kunststoffe und Einwegprodukte und sogar der T-Shirts, die wir verkaufen, um Wege zu finden, verantwortungsvoller zu handeln, ohne die Standards unseres Unternehmens zu gefährden. Wir sind weit davon entfernt, perfekt zu sein, aber wir machen Fortschritte. Wie ich schon sagte, es ist eine Reise.
Zu einem verantwortungsvollen Unternehmen gehört auch Transparenz. Deshalb möchte ich mich in diesem Artikel auf Gitarrenlacke konzentrieren und erklären, wo wir waren, wo wir sind und wo wir hinwollen.
Zunächst einmal sollte ich zugeben, dass das Thema Lackierung unter Gitarrenenthusiasten ein überraschend emotionales Thema sein kann. Glauben Sie mir, wenn Sie eine Debatte unter Gitarrenbauern und eigenwilligen Gitarristen entfachen wollen, gehen Sie in einen Raum und fangen Sie an, über Lacke zu sprechen. Das liegt zum Teil an der langen Geschichte der Lackierung von Saiteninstrumenten, aber auch an der Bandbreite der Meinungen darüber, wie verschiedene Lackierungen den Klang, das Spielgefühl und das Aussehen einer Gitarre beeinflussen.
Mehr als nur eine Lackierung
Gitarren, die die Lackierabteilung in unserer Fabrik in El Cajon, Kalifornien, erreichen, durchlaufen eine Reihe von Prozessen, einschließlich Schleifen, Beizen, Füllen der Maserung und Auftragen der Decklackierung. Betrachten Sie eine gute Lackierung nicht nur als eine Schutzschicht, sondern als ein raffiniertes System, das oft verschiedene Materialien und Technologien enthält, die in einer Abfolge von integrierten Schichten aufgetragen werden, die jeweils eine bestimmte Funktion erfüllen. Zum Beispiel dringt Porenfüller in das Holz ein und stabilisiert es, besonders bei offenporigen Holzarten wie Mahagoni. Eine weitere Lackschicht schützt das Holz und sorgt für das richtige Maß an Dämpfung. (Mehr zum Thema Finish und Dämpfung finden Sie in unserer Sidebar.) Eine weitere Schicht eines Finish-Systems ist der Decklack, der in der Regel mit Blick auf das ästhetische Erscheinungsbild aufgetragen wird und manchmal Maserungen hervorhebt und die Farbkonsistenz verbessert.
Finish-Materialien im Laufe der Jahre
Im Laufe der Jahrhunderte wurden viele verschiedene Materialien für die Endlackierung von hölzernen Musikinstrumenten verwendet, wie z. B. Öle (z. B. Leinsamen oder Tung), Wachse, Schellack (ein Harz, das von der Lackwanze in Indien und Thailand abgesondert wird), Lasuren und verschiedene Lacke. Grundsätzlich bestehen die meisten Lacke aus drei Komponenten: einem Feststoff (z. B. Harz), einem Bindemittel (damit der Lack am Holz und die Feststoffe aneinanderhaften) und einem Träger (z. B. Lösungsmittel, Öl), der das Harz auflöst und es streichfähig macht.
Um die Entwicklung der Gitarrenlacke, einschließlich unseres eigenen, besser zu verstehen, ist es hilfreich, auf die Instrumente zurückzublicken, die ihre Entwicklung beeinflusst haben, wie z. B. die Oud und die Laute. Vor Jahrhunderten wurde das Holz dieser Instrumente mit lokal verfügbaren natürlichen Zutaten wie Glair geschützt, einer Mischung aus Zucker (als Harz für die Haltbarkeit), Eiklar (als Bindemittel) und Honig (als Auftragsmittel, das der Oberfläche auch eine gewisse Flexibilität verleiht). Manchmal wurde auch gehärteter Saft, vielleicht von einem Akazienbaum, eingearbeitet.
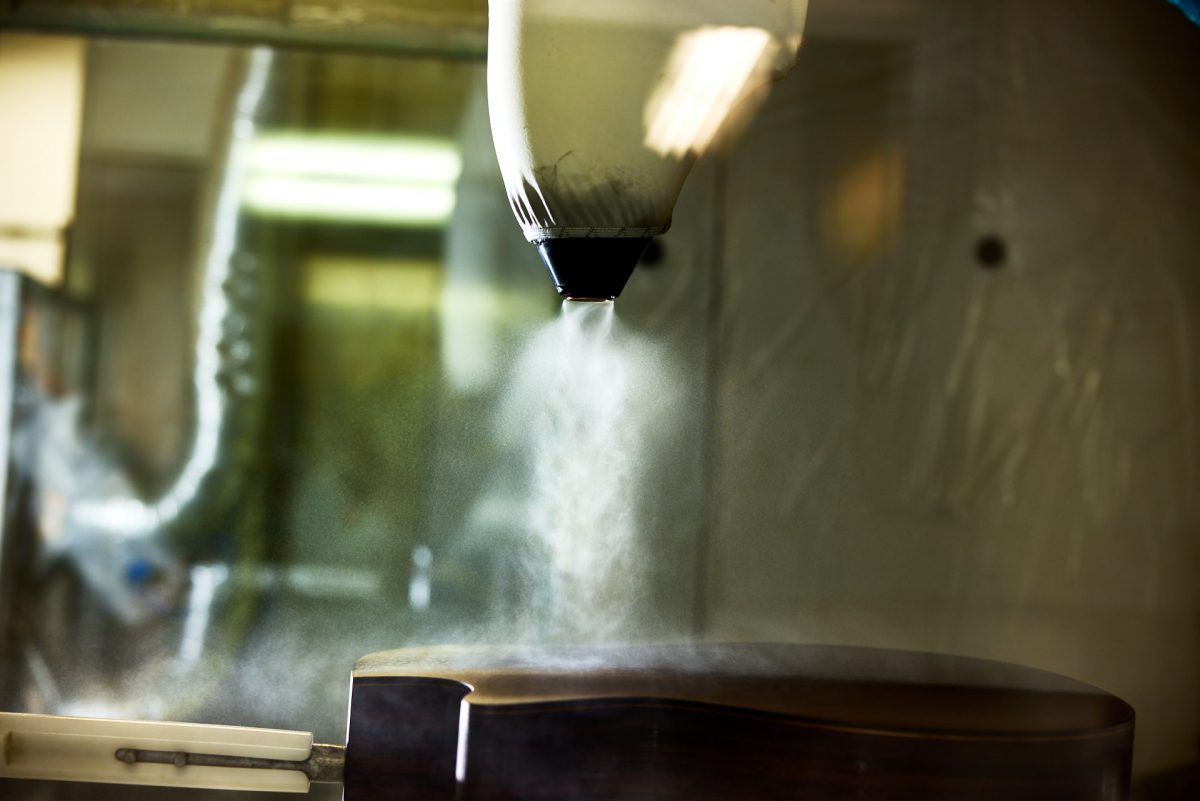
Ein Wort zu Lackstärke und Dämpfung
Es gibt eine eindeutige Korrelation zwischen der Lackdicke und der Dämpfung. Hier bei Taylor haben wir zum Beispiel im Laufe der Jahre mit der Einführung einiger unserer dünneren, klangverbessernden Lacke darüber gesprochen. Zu viel Lack schränkt die Resonanz und Musikalität der Gitarre zu sehr ein. Aber was Sie vielleicht nicht wissen, ist, dass zu wenig Lack – oder gar kein Lack – nicht genug Dämpfungskontrolle bietet, was zu klirrenden Obertönen und manchmal zu einer schrillen akustischen Stimme führen kann. Dämpfung ist also nicht per se eine schlechte Sache, wenn es um den Klang geht.
Schellackpolitur
Die Lackierung von Holzinstrumenten erlebte ihre eigentliche Blütezeit in den 1600er Jahren, wobei die Violine den Ton angab (sowohl wörtlich als auch im übertragenen Sinne) für die nachfolgenden Instrumentenlackierungen. Eine Hochglanz-Holzveredelungstechnik, die sogenannte Schellackpolitur, wanderte in den 1800er und 1900er Jahren von der Geigenwelt zu klassischen und Parlor-Gitarren. Die Technik erhielt ihren Namen von ihrer weit verbreiteten Verwendung in Frankreich durch Möbelhersteller der viktorianischen Ära. Der sehr arbeitsintensive Prozess beinhaltet das Auftragen vieler dünner Schichten von natürlichem Schellack, der vom Lackkäfer abgesondert wird, in denaturiertem Alkohol aufgelöst und mit einem mit Öl versehenen Pad eingerieben wird. Da der Alkohol schnell verdunstet, ist die Trockenzeit zwischen den einzelnen Aufträgen sehr kurz. Der Nachteil ist, dass jede Schicht so dünn ist, dass der Prozess das Auftragen von Hunderten von Schichten erfordert (keine Übertreibung), um diese hochpolierte Oberfläche zu erreichen, die die Leute lieben.
Nitrozelluloselack
1921 erfand das Chemieunternehmen Dupont den Nitrocellulose-Lack für die Automobilindustrie. Der erste moderne, synthetische Lack war haltbar, trocknete innerhalb von Minuten und konnte mit einer Spritzpistole aufgetragen werden, was ihn perfekt für die beginnende Massenproduktion machte. Das Verfahren wurde bald von Holzarbeitern, einschließlich Gitarrenbauern, übernommen.
Nitrolacke haben aber auch Nachteile. Auf der einen Seite lag die Effizienz des Aufbringens mit herkömmlichen Sprühverfahren – also die Menge an Lack, die tatsächlich an der Oberfläche haften bleibt und nicht einfach nur in die Luft verteilt wird – bei nur etwa 10 Prozent. Außerdem benötigen die Lösemittel, die für das Aufbringen auf eine Gitarre aus Holz erforderlich sind, bis zu zwei Wochen Trocknungszeit. Das Ausdünsten dieser Lösemittel kann sogar Monate bis Jahre lang andauern, wodurch die Lackierung dünner, aber dichter wird. Mit Nitrolacken behandelte Oberflächen neigen darüber hinaus im Laufe der Zeit zur Vergilbung und angesichts drastischer Temperaturschwankungen können feine Haarrisse entstehen, die häufig als „Finish-Checking“ bezeichnet werden. Für manche Sammler von Vintage-Gitarren erhöhen diese Haarrisse allerdings den ästhetischen Reiz.
Lösemittel und flüchtige organische Verbindungen (VOC)
Was in den Anfängen des Nitrolacks wenig beachtet wurde, war, dass die verwendeten Lösungsmittel nicht unproblematisch waren. Vor allem, wenn sie mit einer Spritzpistole in einer offenen Werkshalle aufgetragen wurden, setzte Nitro erhebliche Mengen an flüchtigen organischen Verbindungen (VOCs) frei, von denen viele sowohl für die menschliche Gesundheit als auch für die Umwelt gefährlich sind. Ja, VOCs sind allgegenwärtig und kommen auch in der Natur vor. Öffnen Sie eine Flasche Wein und VOCs werden freigesetzt. Es ist nur ein Gas, und manche Gase sind harmlos, andere nicht. Aber die VOCs, die freigesetzt werden, wenn Nitrocelluloselack mit einer Spritzpistole aufgetragen wird, können giftig sein und negative Auswirkungen auf die menschliche Gesundheit haben, einschließlich kurzfristiger Reizungen von Augen, Nase und Rachen, Kurzatmigkeit, Kopfschmerzen, Übelkeit, Schwindel und Hautproblemen. Längerfristige Auswirkungen können Schäden an der Lunge, der Leber, den Nieren oder dem zentralen Nervensystem sein. Nitrozelluloselackierungen werden auch heute noch häufig in verschiedenen Industrien verwendet, darunter auch im Gitarrenbau, wenn auch in einer weitaus sichereren Anwendungsumgebung, um die Arbeiter zu schützen.
Taylor’s Finish Evolution
Im Laufe der Jahre hat der wissenschaftliche Fortschritt in der Welt der Kunststoffe und Polymere neue Formen von Lackierungen hervorgebracht, und einige davon, wie z. B. Konversionslacke, Urethane, Polyurethane, Polyester und Acryl, wurden von der Gitarrenindustrie übernommen. Bei allen handelt es sich einfach um verschiedene Harze, die auf einer sich weiterentwickelnden Wissenschaft basieren, und jedes setzt unterschiedliche Mengen an VOCs frei. Als Taylor Guitars 1974 seine erste Werkstatt eröffnete, übernahm das junge Unternehmen eine Vielzahl von Lackierungen und Applikationsmethoden, die damals in der Branche üblich waren, von Nitrozelluloselack über Konversionslacke bis hin zu Polyurethan. Jede brachte ihre eigenen Umweltprobleme mit sich, mit dem gemeinsamen Nenner einer langen Aushärtungszeit.
Um 1985 stellte Taylor die Lackierung mit Nitrocellulose-Lacken vollständig ein. Im Laufe der Jahre hat das Finish-Team von Taylor seine Prozesse immer wieder radikal verändert und sich von einem sehr manuellen, arbeitsintensiven Ansatz zu einer hochentwickelten, technologiegesteuerten Wissenschaft entwickelt.
Not macht erfinderisch
Bob Taylor war schon immer ein selbstbestimmter Innovator, aber manchmal kann die Motivation auch von außen kommen. So wie der Tag im Jahr 1991, als Bob einen Brief vom Staat Kalifornien erhielt, in dem ihm mitgeteilt wurde, dass Taylor Guitars bald viele der in der Branche üblichen Lackierungen nicht mehr verwenden dürfe. Andere Gitarrenbauer konnten sie verwenden, nur nicht die in Kalifornien ansässigen. Für ein junges Unternehmen mit einer wachsenden Belegschaft muss das eine schwer zu schluckende Pille gewesen sein.
Bob sieht Licht
Nicht lange danach besuchte Bob ein Seminar über die Verwendung von ultraviolettem (UV) Licht, um den Aushärtungsprozess der Lacke zu beschleunigen. Er kehrte in die Fabrik zurück und erklärte: “Das ist der Weg, den wir gehen werden. Ich will alles tun, was nötig ist, damit wir eine saubere, UV-härtende Lackierung für unsere Gitarren entwickeln können.” Das einzige Problem war, dass es die UV-Härtung für dreidimensionale Objekte wie eine Gitarre noch nicht gab, und die Lackhersteller standen nicht gerade Schlange, um einer kleinen Firma in einer obskuren Branche zu helfen. Also stellten wir einen Chemiker ein, der mit Bob und Taylors damaligem Leiter der Lackierabteilung, Steve Baldwin, an der Formulierung eines neuen Lacks und der Entwicklung eines Verfahrens zur Herstellung eines UV-härtbaren Decklacks und Pasten-Füllers arbeitete. In der Zwischenzeit entwarf und baute der Maschinen- und Werkzeugkonstrukteur von Taylor, Matt Guzzetta, einen maßgeschneiderten UV-Härtungsofen, der es ermöglichte, den Lack in 30 Sekunden auszuhärten – im Vergleich zur 12-tägigen Lufttrocknungszeit, die bei Nitrocelluloselack erforderlich ist.
Die neue Lackierung basierte auf Polyester, enthielt weniger Lösungsmittel und reduzierte so schädliche Luftemissionen. Im Gegensatz zu Nitrozelluloselack vergilbte die resultierende Lackierung viel weniger mit und wurde nicht durch Temperaturschwankungen beeinträchtigt. 1995 wurde das Auftragen von UV-härtenden Lacken Teil des Produktionsprozesses, was Taylor zur ersten Gitarrenfirma machte, die ultraviolette Lacke einsetzte. Sie erwiesen sich als haltbarer und ermöglichten einen dünneren Lackauftrag, was auch klangliche Vorteile mit sich brachte. Die extrem verkürzte Trocknungszeit steigerte die Effizienz der Fertigung und führte zu einer drastischen Reduzierung der freigesetzten VOCs.
Erinnern Sie sich an die drei grundlegenden Komponenten herkömmlicher Lacke, die bereits erwähnt wurden: ein Feststoff, ein Bindemittel und ein Lösungsmittel oder Vehikel? Wie Taylor-Gitarrenbaumeister Andy Powers erklärt, war die UV-härtende Lackierung ein Wendepunkt, da diese Technologie die Verwendung von Lösungsmitteln im Wesentlichen überflüssig machte.
“Der UV-Lack hat nur einen Feststoff und ein Bindemittel”, sagt er. “Die beiden Komponenten sind katalysiert und gehen von flüssig in fest über. Es wird kein Lösungsmittel verwendet, um diese streichfähig zu machen. Mit anderen Worten: Der Feststoff und das Bindemittel sind zunächst streichfähig und ändern dann ihren Zustand, sobald sie mit Hilfe von UV-Licht auf der Oberfläche verteilt werden. Die Art und Weise, wie sie weniger Lösungsmittel verwenden, ist also der weitgehende Verzicht auf diese. Das ist auch der Grund, warum wir nicht zehn Schichten sprühen, bei denen 85 Prozent verdunsten; wir sprühen zwei, bei denen fast alles auf der Gitarre verbleibt, außer dem bisschen, das weggeschliffen oder wegpoliert wird.”
Gut für das Unternehmen. Sicher für die Mitarbeiter. Besser für die Umwelt.
Buffy die Gitarrenschlächterin und elektrostatische Anziehung
Der nächste große Fortschritt bei Taylor wurde von dem Wunsch angetrieben, die physische Belastung des manuellen Polierprozesses zu verringern und die Konstanz von Gitarre zu Gitarre zu verbessern. Die Implementierung der neuen Technologie war eine Herausforderung, und die anfänglichen Bemühungen, ein robotergestütztes Poliersystem zu programmieren, brachten der Maschine den Spitznamen “Buffy the Guitar Slayer” ein, aber mit der Zeit fand das Team die Lösung.
Einige Jahre später wurde die Robotertechnologie erneut eingesetzt, dieses Mal für das Lackieren, was zu einer verbesserten Übertragungseffizienz führte, was wiederum weniger Übersprühen und Materialabfall bedeutete. Die Transfereffizienz wurde durch die Einführung der elektrostatischen Anziehungstechnologie zwischen dem Lack und der Gitarre weiter verbessert, die einen Rotationszerstäuber und eine klimatisierte Umgebung zur Optimierung der Lackanziehung umfasst. Letztendlich konnte der Übertragungswirkungsgrad von etwa 15 Prozent beim manuellen Sprühen auf etwa 85 Prozent mit der Roboter-/Elektrostatik-Methode gesteigert werden. Auch hier gilt: weniger VOCs, weniger Abfall, mehr Konstanz und eine sicherere Arbeitsumgebung.
Und fürs Protokoll: Diese neuen Robotertechnologien haben keine Arbeitsplätze ersetzt. Wir haben alle behalten. Wir haben ihnen nur das Leben ein wenig leichter gemacht und den ökologischen Fußabdruck des Unternehmens erheblich reduziert.
Unsere Roboter-Polieranlage ermöglicht ein einheitlicheres Ergebnis und entlastet die Mitarbeiter von der physisch anstrengenden Leistung des manuellen Polierens.
Es geht noch dünner
Mit der Ankunft von Andy Powers im Jahr 2011 begann bei Taylor eine Ära der Entwicklung noch dünnerer Lackierungen (die durch die von uns eingeführten Technologien ermöglicht wurden). Diese neuen Anstrengungen erforderten einen noch disziplinierteren Herstellungsprozess, da eine dünnere Lackierung den Spielraum für eine Fehlerkorrektur in der Fertigung verringert. Bei jeder Lackierung “baut” man nicht mehrere Schichten auf, sondern schleift diese ab, bis Sie das gewünschte Niveau erreichen. Um den Farbton zu verbessern, wollte Andy ein dünneres Finish, und Chris Carter, der Nachfolger von Steve Baldwin, und sein Team halfen uns, die Dicke des Glanzlacks von 6 mils (0,006 inch) auf nur 3,5 mils (0,0035 inch) bei einigen Modellen zu reduzieren. Zum Vergleich: Ein Blatt Büropapier ist 3 mils dick (und falls Sie sich wundern: Wir können die Lackdicke auf einer Gitarre mit einem Ultraschallmessgerät genau messen).
Wasserbasiertes Finish
Seit 2019 verwendet Taylor bei ausgewählten Modellen eine vorkatalysierte wasserbasierte Lackierung. Sie bietet eine starke Haftung beim Auftragen und produziert noch weniger gefährliche VOCs. Viele Gitarristen sagen, dass wasserbasierte Lacke nicht nur umweltfreundlicher sind, sondern sich auch besser anfühlen.
Die Ursprünge der wasserbasierten Lacke bei Taylor Guitars gehen sowohl auf eine zufällige Autofahrt als auch auf die globale Pandemie zurück. Eines Tages fuhr Bob Taylor Chris Carter in seinem neuen Tesla, und die beiden bewunderten das hölzerne Armaturenbrett. Chris vermutete, dass es mit einem Lack auf Wasserbasis behandelt war und versprach, sich darum zu kümmern. Bald darauf begann Chris mit Experimenten und Tests an alten Gitarrenkorpussen. Nach etwa sechs Monaten war er zuversichtlich, dass wir eine alternative, satinierte Lackierung hatten, die sicherer und einfacher zu verwenden war als Konversionslacke. Chris erwähnte es gegenüber Andy Powers, und ein paar Wochen später begann Andy, es auf einem noch unveröffentlichten Prototyp, an dem er arbeitete, zu verwenden. Die Tests erbrachten großartige Ergebnisse.
Dann, am 19. März 2020, löste die COVID-19-Pandemie die unerwartete Schließung der Fabrik aus, gefolgt von der Schließung der Tecate-Fabrik ein paar Tage später. Uns allen wurde gesagt, wir sollten zu Hause bleiben, genau wie den Menschen rund um den Globus. Und eine lustige Sache passierte. Den Leuten wurde langweilig. Und viele von ihnen entstaubten ihre alten Gitarren oder beschlossen, sich eine neue zu kaufen.
Unsere American Dream Series wurde zu dieser Zeit geboren, eine pragmatische Reaktion auf die Realitäten der Rückkehr zur Arbeit und des Gitarrenbaus während einer Pandemie, als die Lieferketten unterbrochen und unvorhersehbar waren. Um es kurz zu machen: Nach einem kurzen Blick auf unseren vorhandenen Holzbestand begannen Bob und Andy darüber zu reden, “mit dem zu kochen, was in der Speisekammer ist” und eine Gebrauchsgitarre zu bauen, mit Massivholzkonstruktion und Taylors V-Class-Bracing, aber auch etwas, das in den USA produziert und erschwinglicher verkauft werden könnte. Die daraus resultierenden “American Dream”-Gitarren waren ein großer Erfolg, aber weniger diskutiert wurde der Sprung nach vorne, den Taylor zu dieser Zeit mit wasserbasierten Lackierungen machte.
Als kleine Teams, unter neuen Sicherheits- und sozialen Distanzierungsnormen, in die Fabrik zurückkehren konnten, standen sie unter Druck. Wir mussten als Unternehmen überleben, und wir mussten mit weniger mehr erreichen. Ein schnellerer, weniger arbeitsintensiver Endbearbeitungsprozess würde helfen, und Chris und sein Team waren mit einer neuen wasserbasierten Lackierung zur Stelle, die schließlich für mehrere der neuen American Dream-Modelle und auch für die neue GT Urban Ash-Gitarre verwendet wurde. Es war ein sofortiger Erfolg und galt als haltbarer als ein Konversionslack. Und auch der Anwendungsprozess war umweltfreundlicher.
Weniger ist mehr
In früheren Wood&Steel-Artikeln habe ich bereits erwähnt, dass der erste, wichtigste und oft am meisten übersehene Aspekt der Nachhaltigkeit die Effizienz ist. Der einfache Akt, weniger zu verbrauchen. Und Taylors kontinuierliche Innovationen bei der Gitarrenlackierung sind ein gutes Beispiel dafür. Die immer strengeren Umweltauflagen in Kalifornien spornten uns zur Entwicklung eines saubereren, dünneren, UV-gehärteten Polyesterlacks an. Eine Initiative, um die physische Belastung des manuellen Polierprozesses zu verringern (und die Konsistenz zu erhöhen), führte zur Ära des robotergestützten Polierens und Sprühens, was zu einer verbesserten Transfereffizienz führte. Eine Fahrt in Bobs Tesla, gefolgt von einer Pandemie, beschleunigte die Einführung von Lacken auf Wasserbasis. All das führt dazu, dass wir sicherere Materialien verwenden und weniger von ihnen. Besser für Taylor Guitars. Besser für die Menschen, die hier arbeiten. Besser für die Umwelt. Und besser für die Gitarristen.