Editor’s Note: In celebration of Taylor’s 50th anniversary year, we’re looking back on some of our most impactful guitar designs. Without question, the GS Mini, introduced in 2010, deserves a bright spotlight, having become one of the most enduringly popular Taylor models in our history — and one of the most broadly appealing acoustic guitars in the world. In just our 14th year of production, we’ve now officially passed the milestone of 500,000 GS Minis made. We thought it would be fun to tap into the Wood&Steel archives and republish the original cover story from our summer 2010 edition, in which we unveiled the guitar.
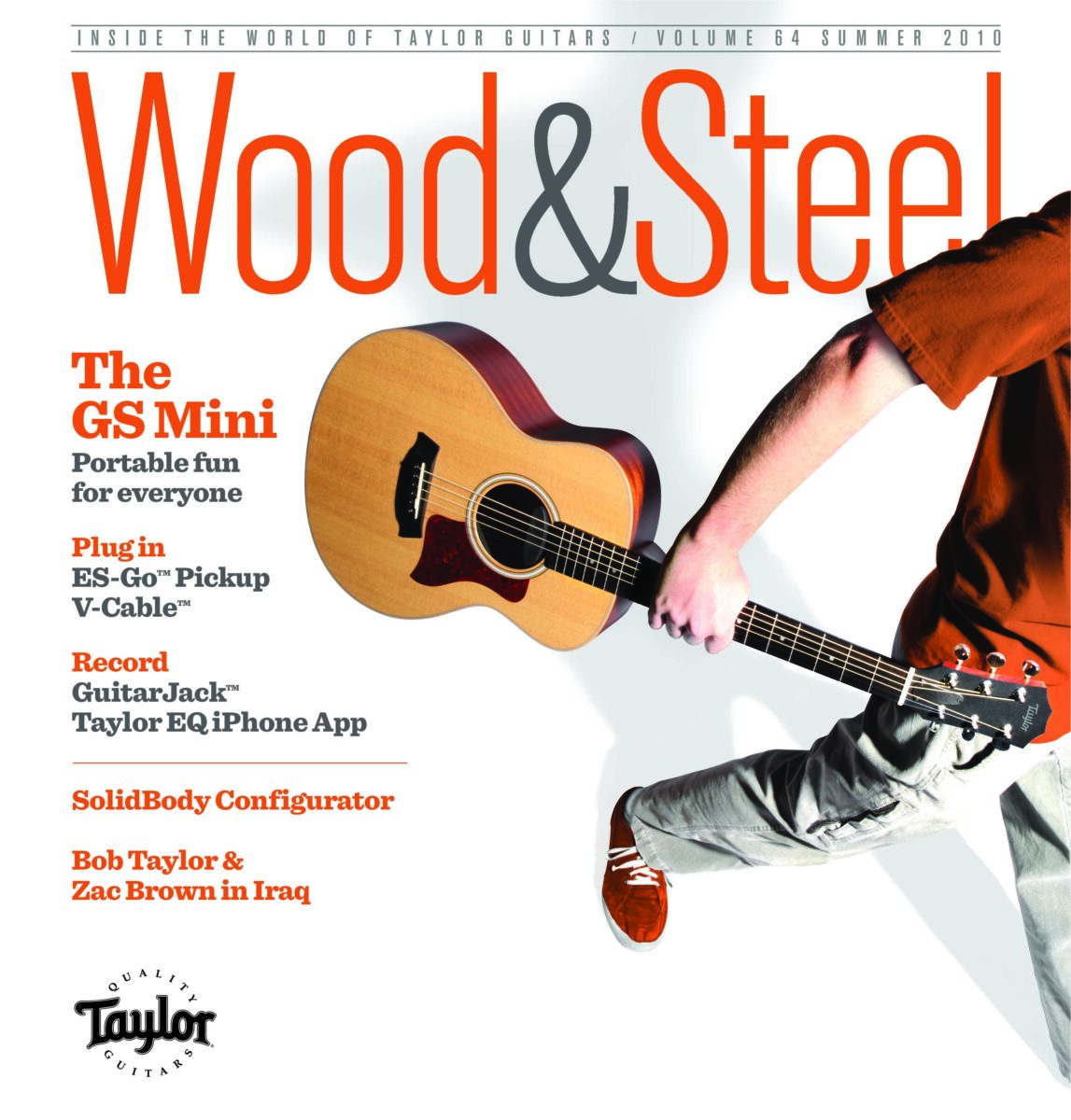
There’s a lot of insightful commentary from Bob Taylor about his design vision for the guitar and the behind-the-scenes R&D that brought it to life. As Bob details, it began with the idea to create a next-generation version of another iconic Taylor design — the three-quarter-size Baby Taylor, which helped legitimize the notion of a travel/child’s guitar as a quality musical instrument. The story offers a fascinating snapshot of where the company was at the time, and as Bob explains, how design and tooling innovations at Taylor often provide a creative platform for other future designs. The original story has been edited for length.
The Mighty GS Mini
From the couch to the campfire to the concert hall, the new GS Mini promises big fun for everyone. Introducing a small-size guitar with a full-size sound.
It was nearly 15 years ago that Taylor’s “subcompact,” three-quarter-size dreadnought, the Baby Taylor, was officially delivered to the world. The pint-size picking machine made its debut back in 1996 as Bob Taylor’s answer to customer requests for a quality, budget-friendly, scaled-down guitar. At the time, an assortment of travel-size guitar surrogates were floating around the market, but as almost anyone would reasonably concede, the “real instrument” quality just wasn’t there. Bob talked about it back in the Winter ’96 issue of Wood&Steel, in the cover story that introduced the Baby.
“For the entire 21 years of Taylor’s existence, I’ve had people approach me with some variation of, ‘I have a kid, and I want to get him or her a “starter” guitar — something good, but affordable. What do you recommend?’ And my answer always has been, ‘No one makes a guitar that meets that description.’
“I decided to make a mini-guitar that’s shaped like an actual guitar, that’s easy to build, that has all the quality features someone would want on any guitar — good materials, a great neck, a really good fret job, a big sound for its size,” Bob explained. “In other words, something that wouldn’t be a toy.”
One of the pleasant discoveries that accompanied the Baby’s arrival was that the players it was ostensibly made for — children and travelers — would turn out to be a mere subset of a broader range of players and applications.
“We’d get comments like, ‘It sounds and feels so good — when can I get one?’” Bob noted in ’96. “Or, ‘I could play slide guitar on this.’ Or, ‘I want one of these by my bed, so when I get an idea in the middle of the night, I don’t have to go get my guitar out of its case.’ Or, ‘I want one for my daughter and one for me.’”
“You want to find out what the limits are, and to do that you’ve got go past the limits.”
Bob Taylor
Perhaps the soundest proof of the Baby’s enduring appeal has been its steady production and sales numbers over time. Almost 15 years later, even after competitors responded with their own travel guitar models, including cheaper Chinese-made products, the Baby remains the leader in quality and demand. Currently, Taylor produces about 60 a day (not counting the Big Baby).
In retrospect, Bob reflects proudly upon the design spirit and engineering that produced the Baby. Developing a new type of guitar that sounds good, plays well and is affordable demands smart, efficient design. Not only was the guitar itself a success, but the design innovation that went into it would prove to be a creative springboard for other significant Taylor developments as well.
“When I talk about our neck joint design, the Expression System, the T5, and our [layered-wood] models,” Bob says, “I always go back to the Baby, because the Baby was the first guitar we ever used a laser on, the first guitar we ever bolted a heelless neck on, the first guitar we ever used veneered sides and back on, with a pressed back to hold the shape.
“We’ve learned a lot since we’ve made that guitar,” Bob elaborates. “We’ve offered so many new innovations, the factory has really matured, the product line has evolved and grown. Since then, we built a factory in Mexico. I think we had two CNC mills when we first made Babys; now we have 50 of them. We’ve got robotic systems and better lasers.”
With the benefit of all those refinements, after 15 years, Bob felt it was time to use that accumulated design and manufacturing expertise to “up the ante” with the Baby — to give it a bigger, fuller sound without compromising the appeal of a small-size guitar.
Sizing Things Up
It was sometime in the spring of 2009 when, as a side project, Bob began actively pursuing the next generation of mini-guitar. Initially, he explored ways to enhance it using the existing Baby shape. He worked with David Judd, a longtime member of Taylor’s product development team, on a series of über-Baby prototypes.
“We were ‘Frankensteining’ a lot of guitars,” Bob says. “I’d ask David to make a guitar with a paper thin top… a guitar with a much longer fret scale… a guitar where the braces almost don’t exist. We made lighter-topped guitars, like ridiculously light. A lot of times, you push it to the point of absurdity. You want to really find out what the limits are, and to do that you’ve got go past the limits. You have to make a guitar that’s stupidly thin, and then find out, yeah, I was right, that’s too thin. Or find out, ahh, maybe that’s not. What we found is what we always seem to find. Rarely do we have a little surprise like the Grand Concert 12-Fret, where you just change something and it’s a whole new guitar. Usually we find that within the confines of an existing guitar design, no matter how much you hotrod that, it doesn’t change it very much. The basic design — the basic size and string length and the thicknesses that make sense — those things give you 95 percent of your tone. You can tweak it to within an inch of its life, and maybe you eke out a little more tone, but you’re not doubling anything. So, you reach a point of diminishing returns, which we proved by making all these ridiculous Babys. Yeah, they sound better, but only by comparison. It’s not like you could pick one up all by itself and go, ‘Now that’s a guitar,’ y’know? It still kind of sounds like a Baby, maybe a little clearer, a little louder. We’d play the two side-by-side and go, ‘Yeah, that one’s better, but… it’s still a Baby.’ That told us we needed a deeper body, a bigger top, a longer scale.”
Bob decided to work with a scaled-down version of the Grand Symphony (GS) shape (introduced in 2006) because it was a Taylor original and because he felt the shape would be the best option for a more robust voice.
“Usually we find that within the confines of an existing guitar design, no matter how much you hotrod that, it doesn’t change it very much.”
“We made a couple guitars that sounded better and had a longer fret scale, but, really, the size wasn’t enough bigger for it to be in a whole different ballpark,” Bob says.
Part of the challenge was to go bigger without getting too big. The Big Baby, by comparison, was too close to a full-size guitar, and part of the design goal was to preserve the ultra-compact quality that made the Baby so popular. They went back to the drawing board, literally.
“We started drawing bigger guitars,” Bob says. “What we do is take thin plywood and we laser out guitars. We might stick a real neck on it and double-stick-tape a bridge and a pickguard on it, and we put the binding lines in, and we hang it on a wall to just kind of look at it and go, ‘Yeah, it looks like a guitar now.’ It took a few tries to get it bigger, because you don’t always get there in one try; you have this idea of what you want, and you do it, and then you think, well, we did it, but we didn’t really do it yet.”
Taylor’s Larry Breedlove, another key member of the development team, says the body length ultimately grew from 16 inches (the Baby is 15-3/4) to 17-5/8 inches.
Another way Bob and his team enhanced the guitar’s size was to make the body deeper — significantly so. The Baby’s body depth is 3-3/8 inches, while the depth of the new guitar was expanded to 4-1/8, deeper than the Big Baby and nearly as deep as a Grand Concert. The scale length was increased from the Baby’s 22-¾ inches to 23-1/2, with 20 frets to the Baby’s 19. The additional string length, Bob points out, helps add depth to the acoustic tone. (The team experimented with a full-size scale length but found that it didn’t offer an appreciable improvement in tone.)
In this clip from our historical podcast, American Dreamers: 50 Years of Taylor Guitars, Bob Taylor and Kurt Listug reminisce about introducing the GS Mini to the world in 2010.
Bob had another design specification: a full version of Taylor’s patented neck with a heel.
“You just get a huge amount of stability there when you get the heel on the neck — you don’t compromise anything,” he says. “So, this neck is more stable than a Baby. It’s just one of those guitars where you set the neck angle, you ship it out, and it’s just rock solid.”
Like the Baby and Big Baby, the guitar was also designed with a braceless arched back, but a whole new shape was designed to refine the overall aesthetic.
At this point, with the scaled-down GS shape solidified as the defining aesthetic of the guitar, the “GS Mini” was informally adopted around the factory as the name for the guitar. Aesthetically, the GS curves scale down nicely, allowing for the guitar to be shapely despite its relatively small size. There were additional aesthetic details that Bob wanted to apply to the Mini to complete the look of a “real” guitar: an inlaid rosette, a pickguard and inlaid purfling lines in the top. The purfling capability is possible, Bob points out, as a result of new production methods that were developed for Taylor’s SolidBody electric.
“We wouldn’t have been able to do that a few years ago,” Bob says. “You need to have perfect registration for that to be possible, which we have now with our newer manufacturing techniques.”
One other visually notable tone-enhancing difference between the Baby and the Mini is the Mini’s larger soundhole — featuring a four-inch diameter (the same as a full-size Taylor), compared to the Baby’s 3-1/2-inch hole. The Mini also features medium-gauge strings.
Compared side-by-side with the Baby, the Mini is clearly a larger guitar, especially in the lower bout, yet the differential doesn’t seem huge. Until you strum it.
“In terms of its ability to put out sound, it’s twice what a Baby is,” Bob says. “And it’s not just the volume, but also the depth and richness of the tone. It truly sounds like a full-size guitar. And it’s ultra-portable.
“We think this might be the modern-day parlor guitar that people have been asking for.”
“When you first look at it, you think, yeah, that’s a little bit bigger guitar, but then you imagine yourself carrying it on a plane, and once you hang that bag strap on your shoulder, you don’t really know that the guitar back there is a bit bigger than the Baby would’ve been,” Bob says. And he can speak from personal experience, having flown with it on several occasions this past spring, both commercially and with the U.S. military, on his way to and from Iraq on a USO tour with the Zac Brown Band. “It won’t weigh you down, and you can put it in the overhead. In fact, I never even had to put it in the overhead. Everywhere I went, flight attendants just said, ‘Can I hang that in the closet?’ because it’s little — they don’t look at it as something that’s wrecking the interior of their plane. It’s funny, when you board with a bigger guitar, the attendants sometimes give you that look, like, ‘Great, that’s gonna take up our whole closet,’ and you get ‘welcomed’ with an unwelcome sigh. But with this, it was a totally different attitude.”
Bob says the amount of engineering and tooling work that went into the design of the Mini was the equivalent of what would have gone into a whole new full-scale guitar, a whole new shape, or a classical guitar.
“We put that effort into this guitar because we think this might be the modern-day parlor guitar that people have been asking for, and the Mini is even smaller than the parlor guitar we made last year. A lot of people just want the equivalent of that fun little buddy lap dog, and they don’t want spend a lot of money.
“The Mini brings a true, real, cool Taylor guitar to a player who might not otherwise be ready for a Taylor yet, maybe because of age, maybe because of money,” Bob adds. “It also takes the blend of portability and quality to a whole new level for the existing Taylor owner, even the person who has the Baby and has loved it and maybe always wished it had a little more sound.”