Chez Taylor Guitars, nous aimons dire que la pérennité est une aventure de longue haleine, et pas une fin en soi. C’est un état d’esprit ; cela nous empêche de nous reposer sur nos lauriers. Nous sommes ainsi en train de nous pencher sur de nombreux points (au-delà de la question évidente de l’emploi du bois), notamment la consommation d’énergie, le plastique et les produits jetables à usage unique… Même les t-shirts que nous proposons à la vente. Nous cherchons des moyens d’agir de manière plus responsable, sans faire de compromis sur les critères qui ont permis à l’entreprise Taylor de devenir ce qu’elle est. C’est loin d’être parfait, mais nous faisons des progrès. Comme je l’ai dit plus haut, c’est une aventure.
La transparence va de pair avec la responsabilité d’entreprise. Dans cet article, je voulais donc aborder les finitions de guitare et vous décrire notre parcours antérieur, notre situation actuelle et notre destination envisagée.
Je devrais commencer par dire que chez les amateurs de guitare, la finition peut être un sujet étonnamment sensible. Croyez-moi : si vous voulez lancer un débat enflammé entre luthiers et musiciens aux idées bien arrêtées, abordez négligemment le thème des finitions. Cette discorde s’explique en partie par la longue histoire des finitions des instruments à cordes, mais aussi par les diverses opinions quant à la manière dont différentes finitions impactent le son, les sensations et le look d’une guitare.
Bien plus qu’un simple revêtement
Les guitares qui atteignent l’étape de la finition dans notre usine d’El Cajon, en Californie, sont soumises à une succession de procédures : elles sont poncées et teintées, les pores sont comblés et la table reçoit une finition. Une bonne finition ne consiste pas seulement en un revêtement protecteur ; c’est un système sophistiqué, qui incorpore souvent une variété de matériaux et de technologies. De nombreuses couches intégrées, chacune avec une fonction spécifique, sont ainsi appliquées. Par exemple, le bouche-pores pénètre dans le bois et le stabilise, en particulier dans le cas d’espèces à pores ouverts comme l’acajou. Une autre couche de finition permettra de protéger le bois et d’offrir juste ce qu’il faut en termes d’atténuation. (Pour de plus amples informations sur la finition et l’atténuation, veuillez consulter notre colonne latérale.) La finition de la couche supérieure de la table, généralement appliquée en gardant l’esthétique à l’esprit, vient parfois mettre en valeur la structure du grain et rehausser la régularité du coloris.
Les matériaux de finition au fil du temps
Au fil des siècles, on a recouru à de nombreux matériaux différents pour la finition des instruments de musique en bois, notamment des huiles (p. ex. huile de lin ou de tung), des cires, de la gomme-laque (une résine secrétée par une cochenille d’Inde et de Thaïlande), des vernis ou encore diverses laques. Fondamentalement, la plupart des finitions sont composées de trois ingrédients : un élément solide (comme la résine), un liant (pour favoriser l’adhérence de la finition sur le bois, et des composants solides entre eux) et un véhicule (p. ex. solvant, huile) pour contribuer à dissoudre la résine et lui permettre de s’étaler.
Pour mieux comprendre l’évolution des finitions de guitare, y compris des nôtres, il convient de revenir sur les instruments qui ont influencé leur développement, comme l’oud et le luth. Il y a des siècles de cela, le bois de ces instruments était protégé grâce aux ingrédients naturels disponibles à l’échelle locale, telle que la glaire : il s’agissait d’une décoction de sucre (employé comme résine pour la durabilité), de blanc d’œuf (liant) et de miel (véhicule pour l’application, offrant également à la surface une certaine flexibilité). De la sève durcie, provenant peut-être de l’acacia, y aurait potentiellement été incorporée.
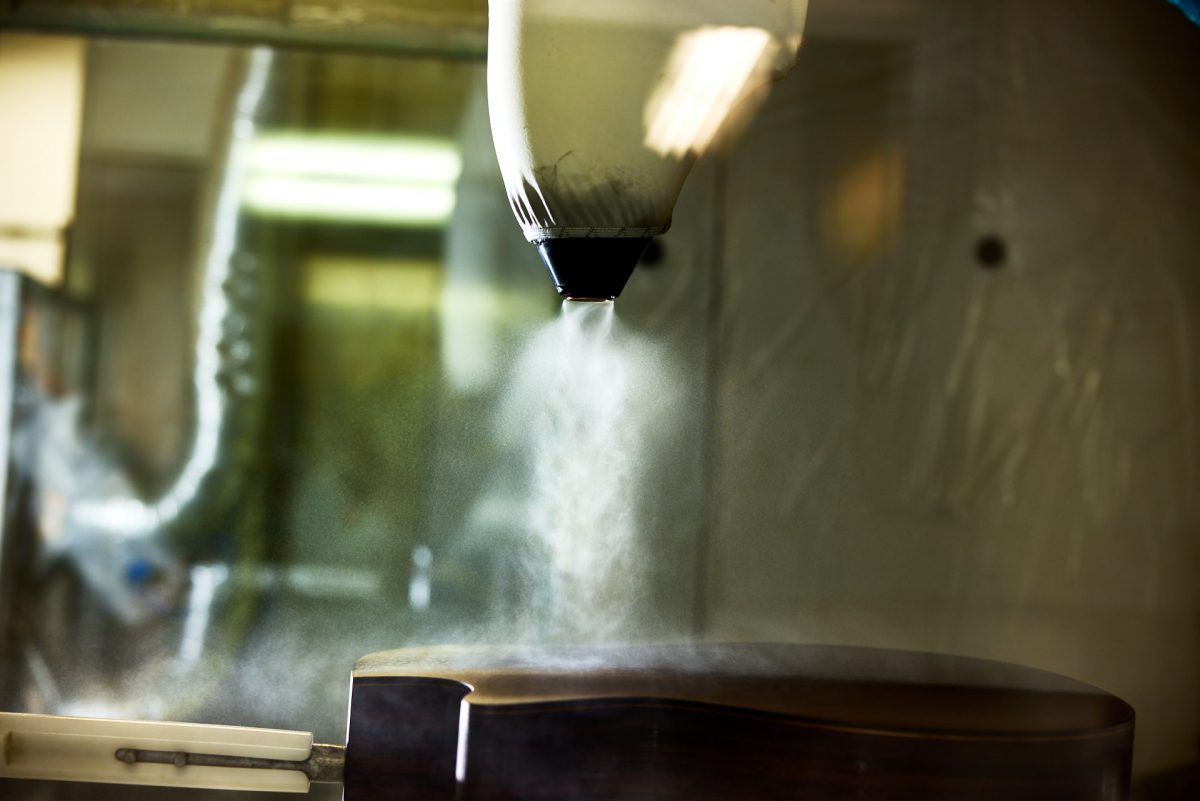
Quelques mots sur l’épaisseur de la finition et l’atténuation
Il existe une véritable corrélation entre l’épaisseur de la finition et l’atténuation. Par exemple, chez Taylor, c’est un sujet que nous avons abordé au fil des années, parallèlement à l’introduction de certaines de nos finitions plus minces, venues améliorer les sonorités de nos instruments. Une finition trop épaisse limitera excessivement la résonnance et la musicalité de la guitare. Toutefois, ce dont vous ne vous rendez peut-être pas compte, c’est qu’une finition trop mince – voire pas de finition du tout – n’offrira pas suffisamment de contrôle sur l’atténuation : votre guitare pourrait délivrer des harmoniques dissonants, et parfois une voix stridente. Par conséquent, l’atténuation n’est pas forcément néfaste lorsqu’elle s’applique aux sonorités.
Vernissage au tampon
La finition des instruments de musique prit véritablement de l’ampleur au XVIIe siècle. Le violon donna le ton (tant au sens propre qu’au sens figuré) pour les finitions qui s’en sont suivies. Le vernissage au tampon (French polishing en anglais, littéralement le « polissage français », NDT), une technique de finition rendant le bois extrêmement brillant, a quitté l’univers des violons pour venir coloniser les guitares classiques et Parlor des XIXe et XXe siècles. La technique tire son nom de son emploi intensif en France par les ébénistes de l’époque victorienne. Ce procédé requiert beaucoup de travail : de la gomme-laque naturelle (une substance sécrétée par la cochenille) dissoute dans de l’alcool dénaturé est appliquée en de nombreuses couches minces, puis frottée au moyen d’un tampon imbibé d’huile. L’alcool s’évapore très rapidement ; ainsi, le temps de séchage entre chaque application est très court. L’inconvénient, c’est que chaque couche est si mince qu’il faut appliquer des centaines de couches (véridique) avant d’obtenir la surface extrêmement brillante tant prisée.
Laque de nitrocellulose
En 1921, l’entreprise de produits chimiques Dupont inventa la laque de nitrocellulose pour le secteur automobile. Première finition synthétique moderne, elle était durable, sèche au toucher en quelques minutes, et pouvait être appliquée au pistolet à peinture : à l’aube de la production de masse, c’était un produit idéal. Ce procédé fut rapidement adopté par les travailleurs du bois, notamment les luthiers.
La laque de nitrocellulose présentait cependant quelques problèmes. Tout d’abord, avec les méthodes de pulvérisation conventionnelles, l’efficacité du transfert (la quantité de finition atteignant sa cible plutôt que de finir dans les airs) était seulement de 10 pour cent environ. Sur une guitare en bois, les solvants requis pour l’application de cette laque nécessitaient plus de deux semaines de séchage à l’air. En réalité, ces émanations de solvants pouvaient perdurer pendant des mois, voire des années, rendant la finition plus mince, mais également plus dense. Au fil des années, les finitions en nitrocellulose ont aussi tendance à jaunir et, en cas de changements importants de température, de minuscules fissures peuvent apparaître. Pour certains collectionneurs de guitares vintage, de telles caractéristiques font partie du charme de l’instrument et le mettent en valeur.
Solvants et COV
Lors du lancement de la laque de nitrocellulose, on ne s’était pas rendu compte que les solvants utilisés allaient poser des problèmes sur certains points. En particulier, si la nitrocellulose était pulvérisée en usine, dans un environnement ouvert, elle libérait des taux importants de composants organiques volatiles (COV). Nombre d’entre eux sont dangereux tant pour la santé humaine que pour l’environnement. Certes, les COV sont omniprésents, et peuvent également être libérés naturellement. Ouvrez une bouteille de vin, et vous serez en présence de COV. Il s’agit simplement d’un gaz ; certains sont inoffensifs, mais d’autres non. Cependant, les COV libérés lorsque la laque de nitrocellulose est appliquée au pulvérisateur peuvent être toxiques et provoquer des effets indésirables sur la santé humaine, notamment une irritation à court terme des yeux, du nez et de la gorge, un essoufflement, des maux de tête, des nausées, des vertiges et des problèmes de peau. Les effets à plus long terme peuvent regrouper des lésions au niveau des poumons, du foie, des reins ou du système nerveux central. Les finitions à base de laque de nitrocellulose sont toujours couramment employées dans plusieurs secteurs, notamment la lutherie, mais dans des conditions d’application bien plus sûres et ce, afin de protéger les employés.
Évolution des finitions chez Taylor
Au fil du temps, les progrès scientifiques dans l’univers des plastiques et des polymères ont donné naissance à de nouvelles formes de finitions ; plusieurs d’entre elles, comme les vernis de conversion, les uréthanes, le polyuréthane, le polyester et l’acrylique, ont été adoptées par les fabricants de guitares. Concernant toutes ces finitions, il s’agit simplement de résines différentes, basées sur les évolutions de la science. Chacune d’entre elles libère un taux de COV qui lui est propre. Quand Taylor Guitars ouvrit boutique pour la première fois en 1974, la jeune entreprise adopta diverses finitions et méthodes d’application couramment employées à l’époque dans le secteur, allant de la laque de nitrocellulose au vernis de conversion, ou, ultérieurement, au polyuréthane. Chacune de ces finitions présentait des problèmes environnementaux qui la caractérisaient intrinsèquement, le dénominateur commun étant un temps de séchage long.
Aux alentours de 1985, Taylor cessa complètement de recourir aux finitions en laque de nitrocellulose. Les années passant, l’équipe Taylor en charge des finitions a continué à modifier radicalement nos procédés, passant d’une approche extrêmement manuelle et laborieuse à une science sophistiquée, basée sur la technologie.
La crise est la mère des inventions
Bob Taylor a toujours été quelqu’un d’autonome et d’inventif ; toutefois, la motivation peut parfois découler d’un facteur externe. Ce fut notamment le cas en 1991, quand Bob reçut une lettre de l’État de Californie l’informant que Taylor Guitars ne serait bientôt plus autorisée à employer un grand nombre des finitions couramment utilisées dans le secteur. Les autres luthiers pourraient y recourir, mais pas ceux implantés en Californie… Pour une entreprise jeune, avec de plus en plus d’employés, la pilule a dû être difficile à avaler.
Bob a une révélation
Peu de temps après, Bob se rendit à un séminaire sur l’emploi de la lumière ultraviolette (UV) pour accélérer le procédé de séchage des finitions. Il revint à l’usine et déclara : « C’est ce que nous devons viser. Je veux faire tout mon possible pour que nous développions une finition plus propre, avec photopolymérisation UV, pour nos guitares ». Le seul problème, c’est que la photopolymérisation UV n’existait pas encore pour les objets en 3D comme les guitares… Et les fabricants de finition ne se bousculaient pas franchement au portillon pour aider une petite entreprise œuvrant dans un secteur obscur. Nous embauchâmes donc un chimiste, qui collabora avec Bob et Steve Baldwin, responsable du service Finitions chez Taylor à l’époque, pour formuler une nouvelle finition et développer un procédé permettant d’obtenir une couche supérieure et un bouche-pores photopolymérisables par UV. Dans le même temps, Matt Guzzetta, concepteur d’outils et de machines chez Taylor, conçut et construisit une unité de photopolymérisation UV sur mesure. Ainsi, la finition était sèche en 30 secondes… Contre les 12 jours de temps de séchage à l’air nécessaires avec la laque de nitrocellulose.
La nouvelle finition était à base de polyester, contenait moins de solvants et diminuait ainsi les émissions nocives dans l’air. À la différence de la laque de nitrocellulose, la finition en résultant était bien moins susceptible de jaunir avec le temps et ne risquait pas de présenter des fissures en cas de fluctuations de température. En 1995, l’application d’une finition avec photopolymérisation UV faisait partie inhérente du processus de production : Taylor fut ainsi la première entreprise à adopter les finitions par ultraviolet. Elles se révélèrent d’ailleurs plus durables. De plus, moins de matériau était nécessaire, ce qui présentait également des avantages sur le plan sonore. La diminution drastique du temps de séchage vint renforcer l’efficacité de fabrication et entraîna une baisse spectaculaire des émanations de COV.
Vous vous souvenez des trois ingrédients fondamentaux des finitions conventionnelles citées plus haut : un élément solide, un liant, et un solvant ou un véhicule ? Comme l’explique Andy Powers, la finition avec photopolymérisation UV était révolutionnaire, car cette technologie éliminait essentiellement le besoin de recourir aux solvants.
« La finition par UV n’emploie qu’un élément solide et un liant », poursuit-il. « Les deux composants sont catalysés et passent de l’état liquide à l’état solide. Aucun solvant n’est nécessaire pour leur permettre de s’étaler. En d’autres termes, l’élément solide et le liant se présentent tout d’abord sous une forme qui s’étale ; leur état évolue dès qu’ils sont répartis sur la surface au moyen de la lumière UV. Ainsi, on utilise moins de solvants, car on en élimine le besoin. C’est aussi pour cette raison que l’on ne pulvérise pas dix couches, dont 85 % s’évaporeraient ; on en pulvérise deux, et la quasi-totalité demeure en place, sauf la minuscule partie qui sera poncée ou polie ».
C’est bien pour l’entreprise. C’est plus sûr pour les employés. C’est mieux pour l’environnement.
« Buffy the Guitar Slayer » et l’attraction électrostatique
La grande avancée qui suivit chez Taylor fut motivée par une volonté de soulager la contrainte physique liée au processus de polissage manuel et d’améliorer l’uniformité d’une guitare à l’autre. La mise en place d’une nouvelle technologie était un défi, et les premiers efforts visant à programmer un système de polissage robotisé nous poussèrent à l’affubler du surnom de « Buffy the Guitar Slayer » [jeu de mots sur le verbe to buff, « polir », et la série « Buffy contre les vampires », en anglais Buffy the Vampire Slayer, NDT]… Au fil du temps, l’équipe parvint à remédier au problème.
Plusieurs années plus tard, la technologie robotique fut à nouveau employée, cette fois-ci pour la pulvérisation des finitions. Le résultat ? Un transfert plus efficace et, en retour, moins de pulvérisation hors cible et de gaspillage de matériaux. L’efficacité du transfert fut en outre améliorée grâce à l’adoption de la technologie d’attraction électrostatique entre la finition et la guitare : elle intègre un atomiseur rotatif et un environnement à la température contrôlée pour optimiser l’attraction de la finition. Au final, l’efficacité du transfert passa de 15 pour cent environ avec la pulvérisation manuelle, à près de 85 pour cent avec la méthode robotisée/électrostatique. Là encore, moins de COV, moins de gaspillage, plus d’uniformité et un lieu de travail plus sûr.
Et que cela soit dit : ces nouvelles technologies robotiques n’ont remplacé aucun employé. Nous avons gardé tout notre personnel. Nous lui avons juste un peu facilité la vie et avons grandement réduit l’empreinte environnementale de l’entreprise.
Notre système de polissage robotisé contribue à une meilleure uniformité et permet de ne plus recourir au polissage manuel, très exigeant physiquement
Encore plus mince
Chez Taylor, l’arrivée d’Andy Powers en 2011 coïncida avec le début d’une ère marquée par le développement de finitions encore plus minces. Ces efforts révolutionnaires nécessitèrent un procédé de fabrication encore plus strict : en effet, cette finition encore plus mince réduit votre marge d’erreur au niveau de la fabrication. Quelle que soit la finition, vous n’« accumulez » pas de multiples couches ; au lieu de cela, vous poncez jusqu’à atteindre le niveau désiré. À des fins d’améliorations sonores, Andy voulait une finition plus mince. Avec son équipe, Chris Carter, le successeur de Steve Baldwin, contribua à réduire l’épaisseur de notre finition brillante, passant de 6 mils (0,15 mm) à 3,5 mils (0,09 mm) sur certains modèles. Pour vous donner une idée, une feuille de papier standard mesure 0,08 mm d’épaisseur. (Et au cas où vous vous poseriez la question, on peut mesurer précisément l’épaisseur d’une finition sur une guitare à l’aide d’une jauge à ultrasons).
Finition à base d’eau
En 2019, Taylor commença à employer une finition précatalysée à base d’eau sur certains modèles. Cette dernière offre une forte adhérence lors de l’application, et émet encore moins de COV nocifs. Outre le fait qu’elle soit encore plus respectueuse de l’environnement, de nombreux musiciens déclarent que les finitions à base d’eau sont plus agréables au toucher.
Chez Taylor Guitars, un trajet fortuit en voiture et une pandémie mondiale sont à l’origine des finitions à base d’eau. Alors que Bob Taylor était au volant de sa nouvelle Tesla, accompagné de Chris Carter, les deux hommes admiraient le tableau de bord en bois. Chris pensait qu’il avait reçu une finition à base d’eau, et promit à Bob de se pencher sur la question. Peu de temps après, Chris commença à faire des expériences et à mener des tests sur des corps de guitares ayant été mis au rebut. Environ six mois plus tard, il était confiant : nous possédions une finition satinée alternative, plus sûre et plus facile à employer que le vernis de conversion. Chris en parla à Andy Powers et, quelques semaines plus tard, Andy commença à s’en servir sur un prototype encore secret sur lequel il travaillait. Les tests donnèrent d’excellents résultats.
Malheureusement, le 19 mars 2020, la pandémie de COVID-19 imposa la fermeture inattendue de l’usine d’El Cajon, suivie quelques jours plus tard par la fermeture de celle de Tecate. On nous demanda de rentrer chez nous, purement et simplement, comme tout le monde sur cette planète. Survint alors quelque chose d’improbable… Les gens commencèrent à s’ennuyer. Nombre d’entre eux dépoussiérèrent leur vieille guitare ou décidèrent d’en acheter une nouvelle.
Notre série American Dream naquit à cette époque : elle constituait une réaction pragmatique face à la réalité du retour au travail et de la fabrication de guitares en plein cœur d’une pandémie, alors que les chaînes d’approvisionnement étaient perturbées et les livraisons imprévisibles. Pour résumer, après avoir jeté un rapide coup d’œil à notre stock de bois, Bob et Andy commencèrent à évoquer l’idée de « faire avec ce qu’il y avait dans les placards » et de fabriquer une guitare fonctionnelle, dotée de la construction en bois massif et du barrage V-Class de Taylor, mais qui serait produite aux États-Unis et proposée à un prix plus abordable. Les guitares American Dream nées de cette démarche rencontrèrent un immense succès. Toutefois, on parla moins du grand pas en avant que fit Taylor à l’époque en recourant aux finitions à base d’eau.
Lorsque les équipes à effectif réduit furent autorisées à revenir à l’usine, en respectant de nouvelles normes de sécurité et de distanciation sociale, elles étaient sous pression. Nous devions survivre en tant qu’entreprise, et nous devions faire le maximum avec le minimum. Un procédé de finition plus rapide et moins laborieux serait bénéfique, et Chris et son équipe étaient prêts : leur nouvelle finition à base d’eau fut finalement appliquée sur plusieurs des nouveaux modèles d’American Dream, ainsi que sur la nouvelle GT Urban Ash. Le succès fut immédiat : cette finition fut considérée comme plus durable qu’un vernis de conversion. De plus, le procédé d’application était plus respectueux de l’environnement.
La sobriété est la clé du succès
Dans de précédents articles de Wood&Steel, j’ai mentionné que le premier aspect le plus important, et souvent le plus ignoré, de la pérennité, c’était l’efficacité. Tout simplement, le fait d’utiliser moins de choses. Les innovations de Taylor en matière de finitions de guitares en sont un bon exemple. En Californie, les réglementations environnementales toujours plus nombreuses ont motivé l’élaboration d’une finition polyester plus propre, plus mince et photopolymérisée par UV. Une initiative destinée à soulager la contrainte physique du procédé de polissage manuel (et accroître l’uniformité) a ouvert la voie à une ère de robotisation du polissage et de la pulvérisation, entraînant une meilleure efficacité du transfert. Un tour dans la Tesla de Bob, suivi d’une pandémie, a accéléré notre adoption des finitions à base d’eau. Toutes ces actions nous ont poussés à employer des matériaux plus sûrs… Et surtout, moins de matériaux. C’est mieux pour Taylor Guitars. C’est mieux pour nos employés. C’est mieux pour l’environnement. Et c’est mieux pour les musiciens.