An armrest on an acoustic guitar is a thing of beauty. It marries form and function in a way that offers the practical benefit of a more ergonomic playing experience while also elevating the aesthetic appeal of the instrument. Between its sculptural contours, visually striking woods, and in many cases, decorative purfling lines topped with a glossy finish, an armrest can transform a guitar into a piece of playable, musical art — especially in the hands of our talented craftspeople.
Our guitar lineup features three styles of armrests: a beveled armrest, with its elegantly sloped surface, showcased through our ultra-premium Custom program and on several Builder’s Edition models; a radius armrest, featuring a rounder softening of the body edge and built into our Presentation, 900 and 800 Series; and a simplified, production-friendly bevel-like armrest on our entry-level Academy Series guitars made in Tecate — because we think a developing player has the most to gain from the extra playing comfort.
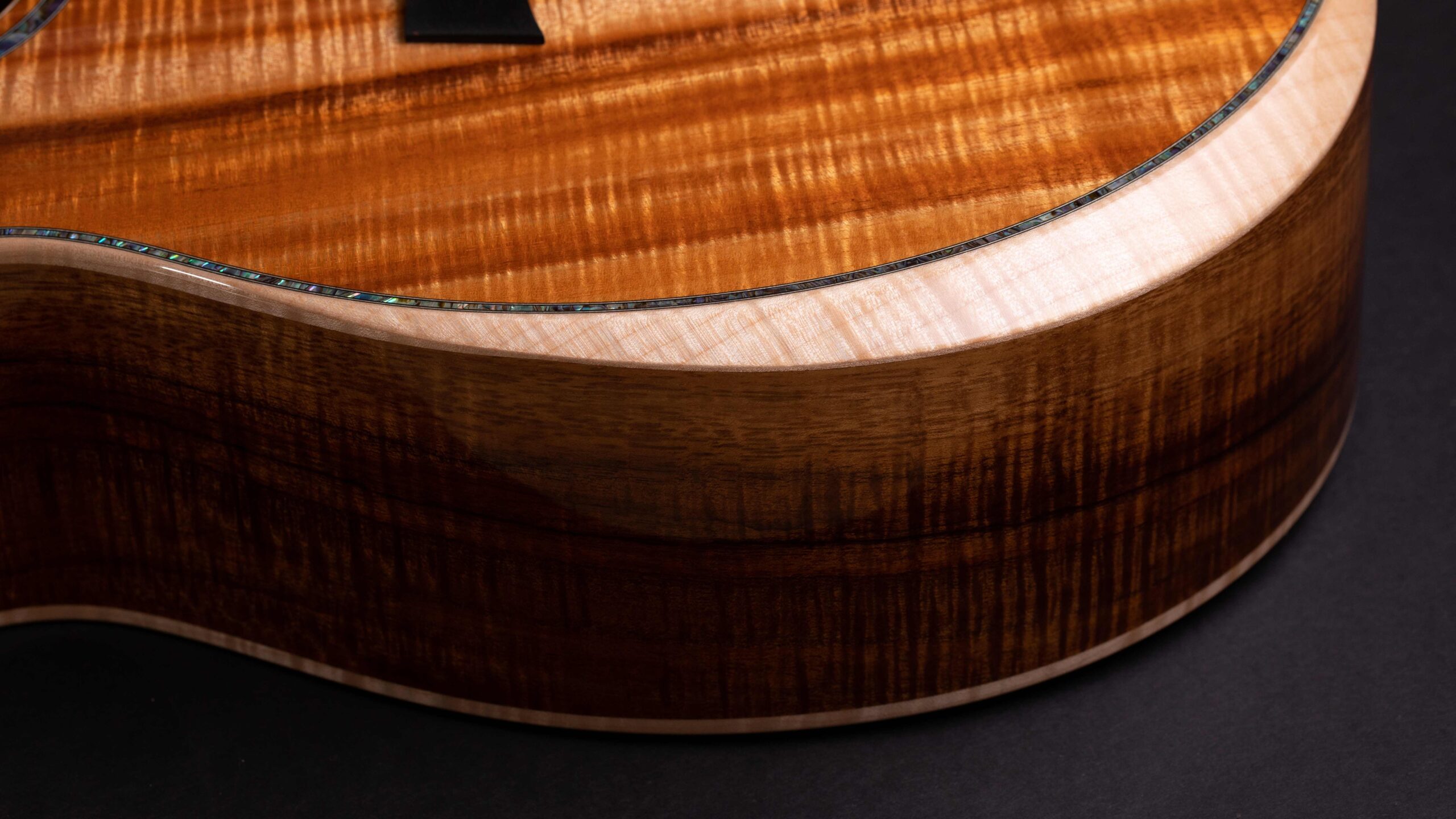
Beveled Armrest
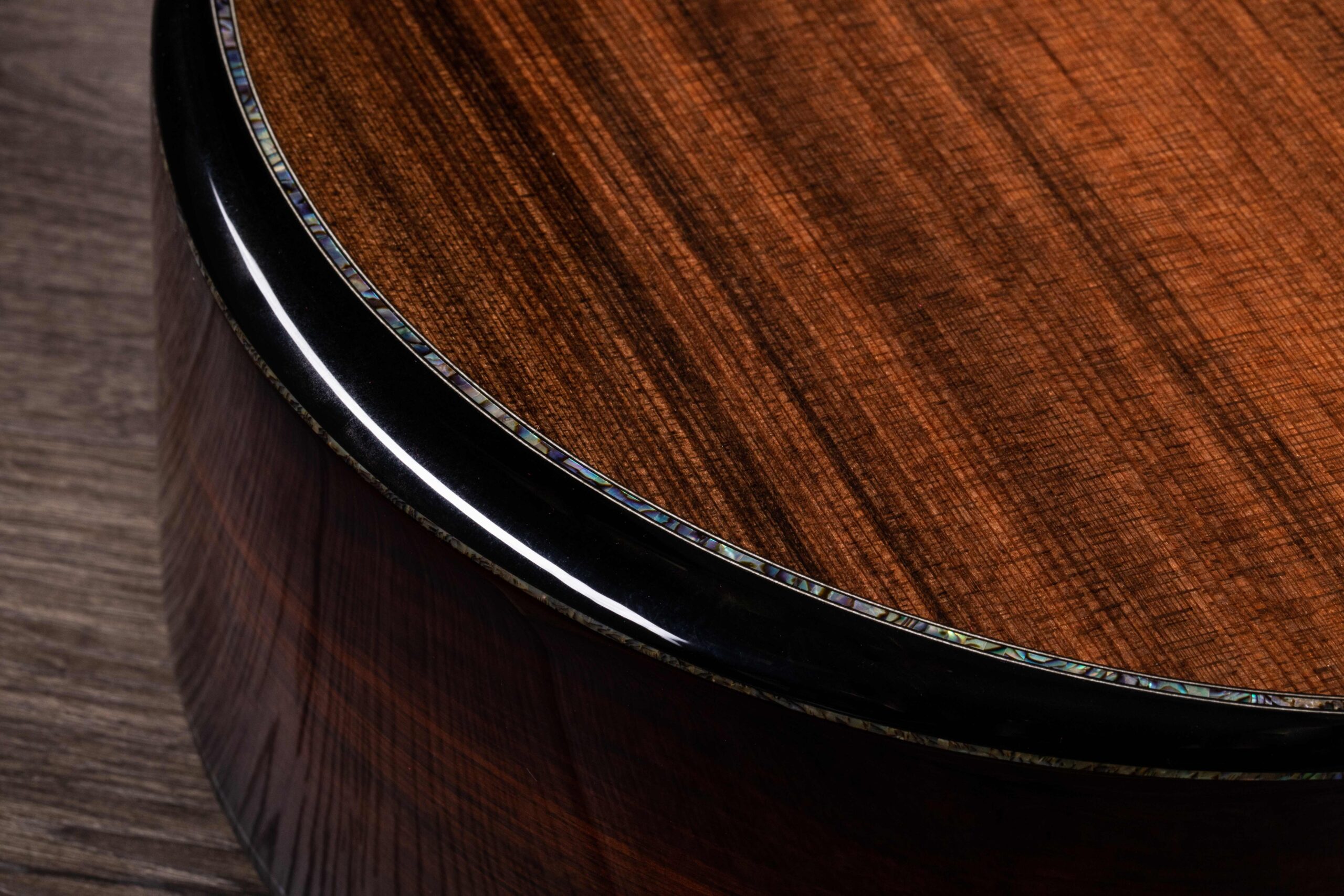
Radius Armrest
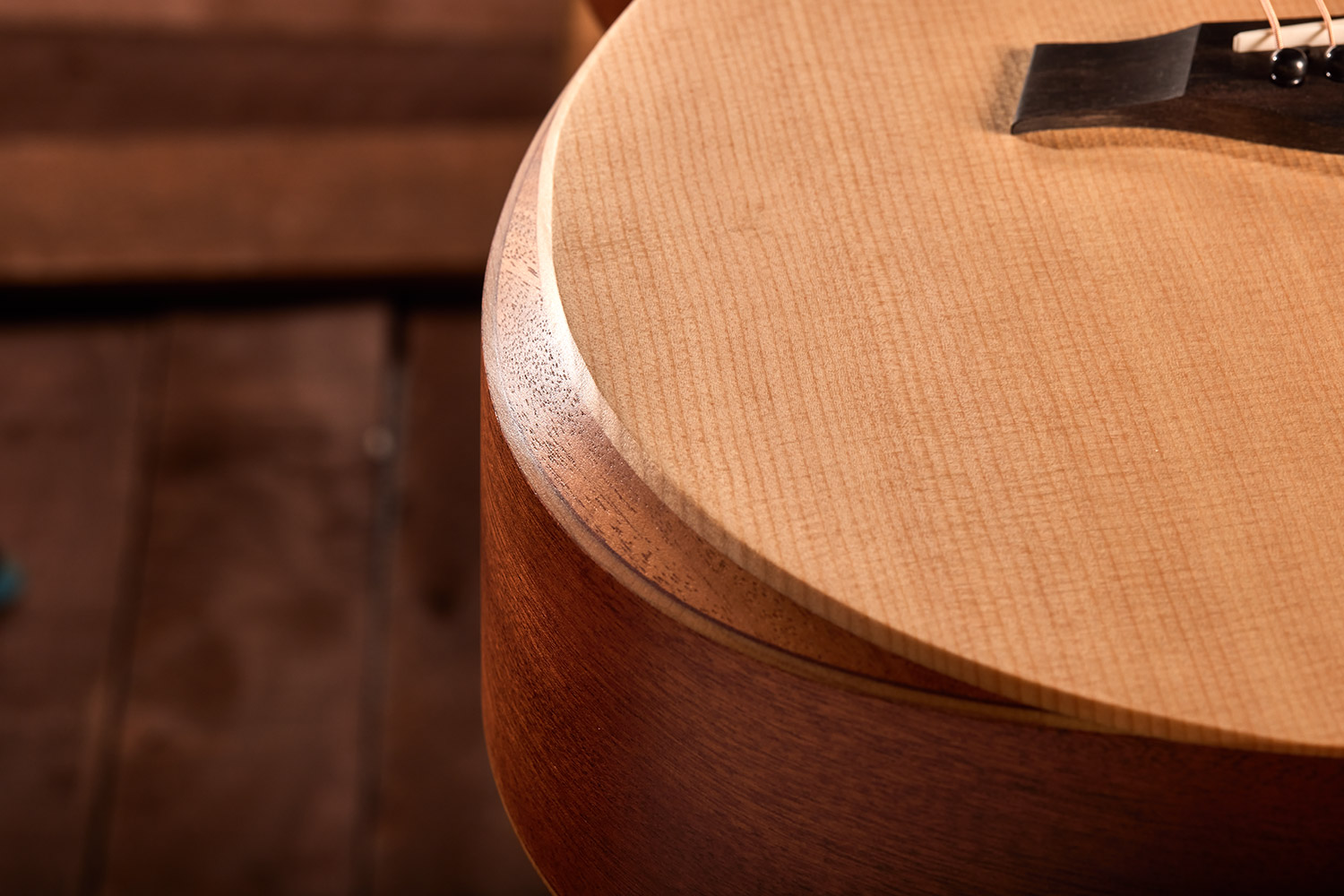
Bevel-like Armrest
High-end Hand Craftsmanship
Though the world may know Taylor as a production-level manufacturer, the truth is that there is an extraordinary amount of skilled handwork that goes into each guitar we make. And the skill level required to execute the beveled armrests we make for some of our custom models at our El Cajon factory is exceptional.
“It’s a practice in focus and patience,” says chief designer Andy Powers, who speaks from experience.
“It requires the utmost attention to detail, as we are essentially teasing all these components — tiny purfling pieces, compound glue surfaces, and bent veneers — into a perfectly blended piece of wood sculpture,” he says. “And it demands flawless sanding at the end, with the risk of potentially ruining all the work that came before it. Despite the huge effort, the results are worth it.”
One clarifying note about the beveled-armrest guitars made in El Cajon: We actually make two versions. Custom models built with an armrest demand the highest level of individual skill because they incorporate a veneer and are hand-carved. The armrests featured on our Builder’s Edition models are slightly more production-friendly and benefit from additional tooling (developed in-house) that allows us to CNC-machine the mahogany armrest piece. The armrest is also finished without an additional wood veneer.
We’ll share some of the steps required to produce a beveled and radius armrest below, but truthfully, you need to see the process to fully appreciate it. While it would be a bit tedious to show you every step, we wanted to bring you some highlights, especially for a custom beveled armrest. Here, we see a custom Grand Auditorium body featuring beautiful figured koa as an armrest is crafted and topped with a veneer of figured maple.
Making a Custom Beveled Armrest
The process begins in our Sidebending department after the sides are bent and glued together to form the outline of the guitar body. Normally, slotted kerfing strips are added to the interior edges of the sides to provide a wider glue surface for the top and back to be secured. For an armrest guitar, a CNC-machined piece of solid mahogany is glued in the area of the lower bout where the armrest will be located. This will supply the wood material that will later be carved into proper shape.
After the top and back are glued in place, the binding and purfling slots are routed into the body. Next, a pair of custom jigs — a separate set exists for each different body shape — is used to locate the exact position of the top and side purfling inlay slots that will border the armrest. One is used for the top cut; the other for the side purfling that will run along the bass side of lower bout. Each jig will be vacuum-secured to the body. Once the slots are routed, the slot edges are blended into the purfling slot previously cut for the rest of the body to create a smooth transition.
The binding and purfling inlay processes are similar to our standard installation techniques, although the top inlay can be more complex for a custom guitar, perhaps featuring colorful abalone shell framed by pinstriped purfling lines and then the wood binding or armrest material. All the purfling lines will be inlaid before the armrest is sculpted.
A two-sided Japanese rasp is used to manually carve and shape the contours. The majority of the wood is removed using the coarse side; the finer side is used later in the process, followed by a round of nuanced shaping with a file. A straight edge is used to inspect the level of the armrest surface, and if necessary, a scraper is used to make any additional refinements. A sanding block is used to create an ultra-smooth final contour. From there, a laser-cut wood veneer that has been color-matched with the binding (the same species of wood) is glued in place. Any excess veneer material is then scraped away, followed by additional sanding.
Making a Radius Armest
Our radius armrest made its debut in 2017 with the introduction of our 800 Deluxe Series. (That series was later discontinued when we streamlined our guitar line, but that armrest became a standard feature of our 800, 900 and Presentation Series.)
Compared to the sloped chamfer of the beveled armrest, the radius features a slightly narrower and rounder softening of the edge in the lower bout area. On the 800 Series, the armrest incorporates a rosewood insert to echo the rosewood-centric aesthetic of the flagship series. The insert is shaped into a sleek contour whose tapered ends transition into maple binding (accented with rosewood top trim). For the 900 Series, the armrest and binding are made of ebony with paua shell and koa trim. The Presentation Series features an ebony armrest and binding with paua edge trim frame with ultra-thin black and white purfling lines.
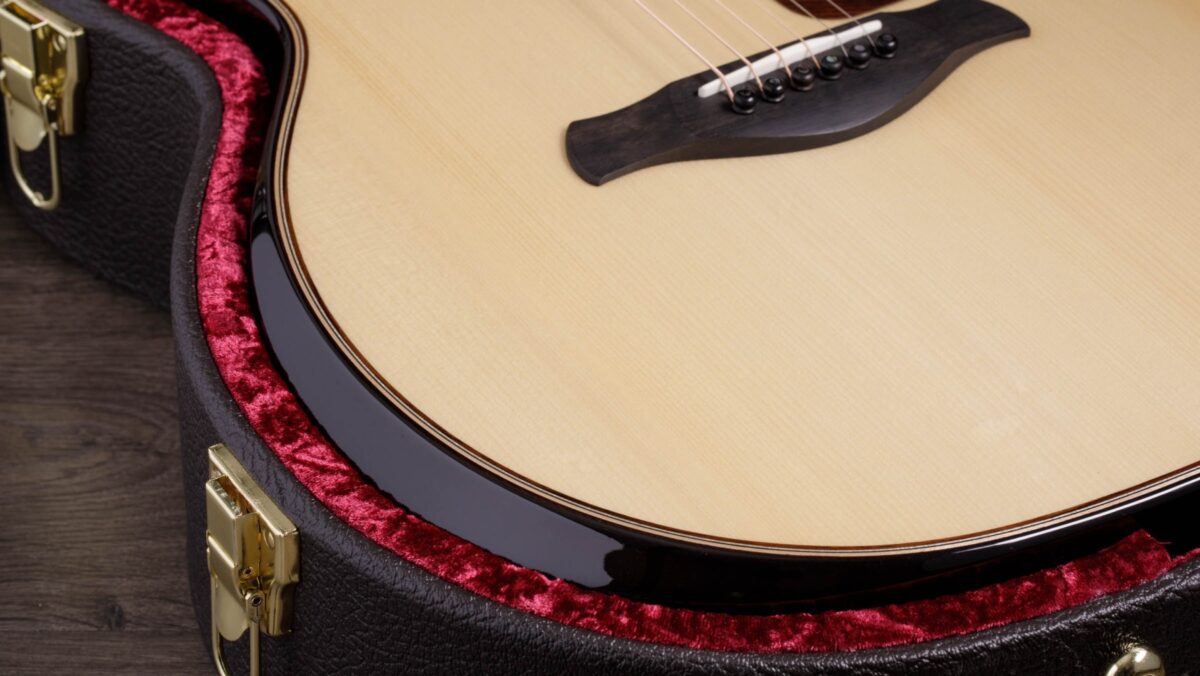