En Taylor Guitars nos gusta decir que la sostenibilidad es un viaje, no un destino. Esta filosofía evita que caigamos en la complacencia y nos permite centrarnos en una serie de cuestiones que van más allá del tema obvio del consumo de madera para abarcar aspectos como el uso de energía, los plásticos, los productos desechables de un solo uso e incluso las camisetas que vendemos. El objetivo es encontrar estrategias para actuar de forma más responsable sin comprometer los estándares en los que se fundamenta la empresa. Por supuesto, no hemos llegado a la perfección, pero vamos avanzando. Como decía, esto es un viaje.
Un elemento importante en una compañía que quiere ser responsable es la transparencia. Por lo tanto, he querido centrar este artículo en los acabados de las guitarras para explicar de dónde venimos, dónde estamos y a dónde queremos llegar.
Para empezar, señalemos que los entusiastas de la guitarra se toman el tema del acabado de una forma sorprendentemente visceral. Creedme: si queréis azuzar un encendido debate entre luthiers e intérpretes testarudos, simplemente tenéis que sacar el tema de los acabados. En parte, esto se debe a la larga historia de los acabados para instrumentos de cuerda, pero también a la variedad de opiniones sobre cómo los distintos acabados afectan al sonido, la sensación y el aspecto de una guitarra.
Mucho más que un revestimiento
Las guitarras que llegan al departamento de acabados de nuestra fábrica de El Cajón (California) pasan por una serie de procesos que incluyen el lijado, el tinte, el tapado de poros y la aplicación de la capa superior. Un buen acabado no es un simple revestimiento protector, sino un sistema refinado que suele incluir diferentes tecnologías y materiales aplicados en una sucesión de capas integradas con funciones individuales específicas. Por ejemplo, el tapaporos penetra en la madera para estabilizarla, lo cual es particularmente importante en especies de poro abierto como la caoba. La aplicación de otra capa de acabado protegerá la madera y proporcionará el nivel de amortiguación adecuado. (En el recuadro encontrarás más información acerca de la relación entre el acabado y la amortiguación). Otra de las capas de un sistema de acabado es el revestimiento superior, que normalmente se aplica pensando en el aspecto estético y con la idea de resaltar los patrones de veteado o de uniformizar el color.
Breve historia de los materiales para el acabado
Durante siglos, se han utilizado muchos materiales diferentes para el acabado de instrumentos musicales de madera, como aceites (por ejemplo, de linaza o de tung), ceras, goma laca (una resina secretada por una especie de gusano nativa de la India y Tailandia), barnices y varios tipos de lacas. En esencia, la mayoría de los acabados tienen tres componentes: una base sólida (como la resina), un aglutinante (para que el acabado se adhiera a la madera y los elementos sólidos se peguen entre sí) y un vehículo (disolvente, aceite, etcétera) que ayuda a disolver la resina para que se pueda extender sobre una superficie.
Para comprender mejor la evolución de los acabados para guitarra, incluido el nuestro, echemos la vista atrás y fijémonos en los instrumentos que influyeron en su desarrollo, como el oud y el laúd. Hace siglos, la madera de estos instrumentos se protegía con ingredientes naturales disponibles a nivel local, como un material resultante de una mezcla de azúcar (utilizada como resina para alargar la durabilidad), clara de huevo (el agente aglutinante) y miel (el vehículo de aplicación, que también le da a la superficie un cierto grado de flexibilidad). A veces también se añadía savia endurecida extraída de árboles del género acacia.
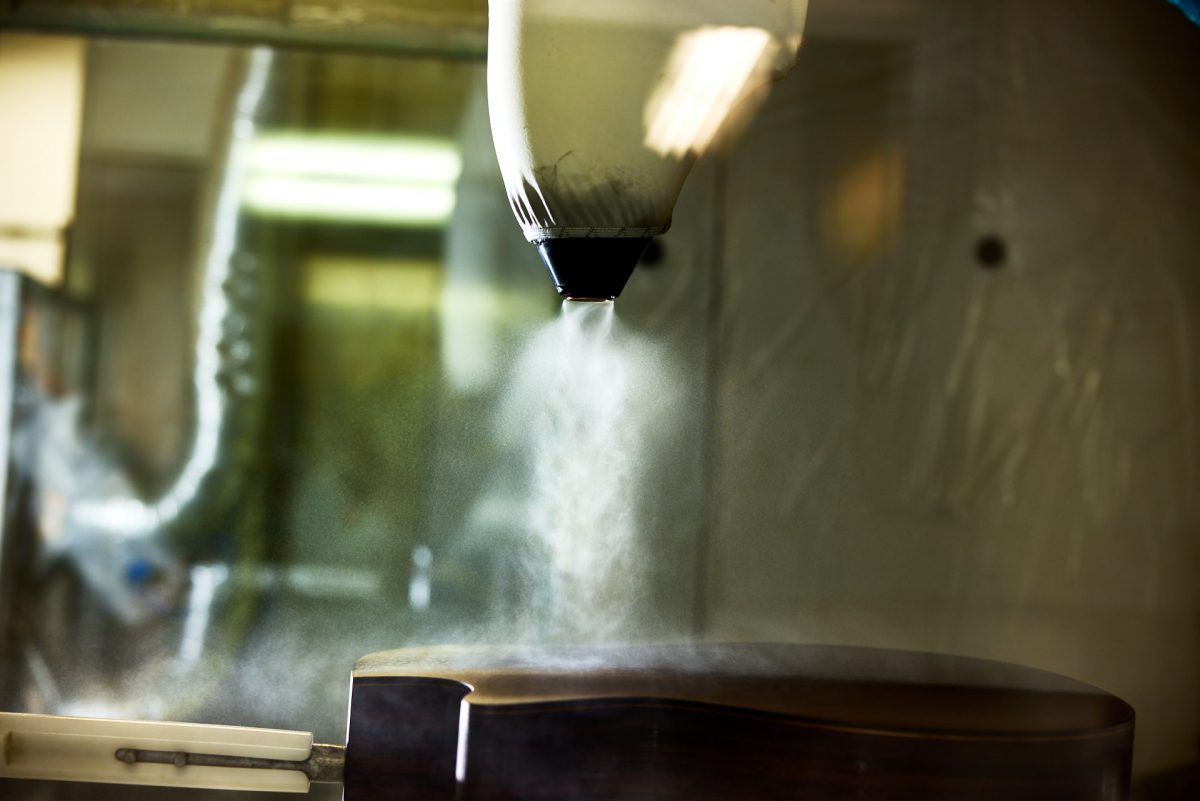
El espesor del acabado y la amortiguación
Existe una relación comprobada entre el espesor del acabado y la amortiguación. En Taylor ya hemos hablado de este tema a medida que hemos ido presentando nuestros acabados más finos, que en última instancia mejoran el tono de la guitarra. Un acabado demasiado grueso ahogará la resonancia y la musicalidad del instrumento. Sin embargo, también hay que pensar que un acabado demasiado sutil (o incluso inexistente) no permitirá controlar correctamente la amortiguación, lo cual puede provocar conflictos de armónicos y, en ocasiones, producir una voz acústica estridente. Moraleja: la amortiguación no es algo intrínsecamente malo en el mundo del sonido.
El pulido francés
Los acabados de los instrumentos de madera alcanzaron la mayoría de edad a partir del siglo XVII, y fue el violín quien marcó el tono (en sentido tanto literal como figurado) de los acabados que se irían desarrollando. Durante los siglos XIX y XX, una técnica de acabado muy brillante llamada «pulido francés» pasó del mundo del violín al de las guitarras clásicas y de salón. Se le dio este nombre porque los fabricantes de muebles franceses lo utilizaron mucho en la época victoriana. El proceso es extremadamente laborioso e implica el uso de muchas capas finas de goma laca natural secretada por el gusano de la laca, disuelta en alcohol desnaturalizado y frotada con una almohadilla lubricada con aceite. El alcohol se evapora rápidamente, de manera que el tiempo de secado entre cada aplicación es muy corto. El inconveniente es que cada revestimiento es tan fino que hay que aplicar cientos de capas (sin exagerar) para lograr esa superficie altamente pulida que al público le encanta.
Laca de nitrocelulosa
En 1921, la empresa de químicos Dupont inventó la laca de nitrocelulosa para su uso en la industria del automóvil. Fue el primer acabado sintético moderno: era duradero, se secaba al tacto en cuestión de minutos y se podía aplicar con una pistola pulverizadora, así que resultaba ideal para los albores de la producción en masa. El proceso pronto fue adoptado por los artesanos de la madera, incluidos los constructores de guitarras.
Sin embargo, la laca de nitrocelulosa también tenía sus inconvenientes. En primer lugar, la eficiencia de transferencia de los métodos de pulverización convencionales (es decir, la cantidad de acabado que realmente llega a la superficie tratada en lugar de quedarse flotando en el aire) era solo de aproximadamente el 10 %. En el caso de una guitarra de madera, los disolventes necesarios para aplicar esta laca requerían más de dos semanas de curado al aire. De hecho, esos disolventes pueden continuar emitiendo gases durante meses e incluso años, de manera que el acabado queda más fino pero más denso. Además, los acabados de nitrocelulosa tienden a amarillear con el tiempo, y la exposición a fluctuaciones de temperatura drásticas puede provocar unas pequeñas grietas conocidas como «craquelado». Para algunos coleccionistas de guitarras vintage, estas características realzan el encanto estético.
Disolventes y COV
En los inicios de la laca de nitrocelulosa, aún no se tenía un conocimiento claro de la parte negativa de los disolventes utilizados. La nitrocelulosa libera niveles significativos de compuestos orgánicos volátiles (COV) que son perjudiciales tanto para la salud humana como para el medio ambiente, sobre todo si se aplica con una pistola pulverizadora en un entorno industrial abierto. Sí, los COV son omnipresentes y también se producen de forma natural. Al abrir una botella de vino, por ejemplo, se liberan COV. Se trata simplemente de gas, pero hay gases inofensivos y otros que no lo son. Los COV que se liberan al aplicar laca de nitrocelulosa con una pistola pulverizadora pueden ser venenosos y provocar efectos adversos para la salud humana, como irritación transitoria de ojos, nariz y garganta, dificultad para respirar, dolor de cabeza, náuseas, mareos y problemas en la piel. Las consecuencias a largo plazo pueden incluir daños en los pulmones, el hígado, los riñones o el sistema nervioso central. Hoy en día todavía se usan habitualmente acabados de laca de nitrocelulosa en varios sectores (incluida la industria de la fabricación de guitarras), aunque se hace en un entorno de aplicación mucho más seguro para proteger a los trabajadores.
La evolución de los acabados en Taylor
A lo largo de los años, los avances científicos en el mundo de los plásticos y los polímeros han dado lugar a nuevos tipos de acabados. La industria de la guitarra ha adoptado varios de ellos, como el barniz de conversión, los uretanos, el poliuretano, el poliéster y el acrílico. En realidad, se trata de diversas resinas que emiten distintos niveles de COV. Cuando Taylor Guitars inició sus operaciones en 1974, la incipiente empresa recurrió a diferentes acabados y métodos de aplicación habituales en aquel momento, desde laca de nitrocelulosa hasta barnices de conversión y, más tarde, poliuretano. Cada uno de ellos traía consigo sus propios problemas ambientales, y todos tenían como denominador común un tiempo de curado muy prolongado.
Hacia 1985, Taylor prescindió por completo de los acabados de laca de nitrocelulosa. Desde entonces, el equipo de acabados de Taylor ha ido transformando radicalmente los procesos de la empresa, pasando de un tratamiento altamente manual y laborioso a un enfoque científico impulsado por tecnología sofisticada.
La crisis es la madre del ingenio
Bob Taylor siempre ha tenido un espíritu muy emprendedor, pero a veces la motivación para innovar puede venir de fuentes externas. Por ejemplo, del día de 1991 en que Bob recibió una carta del Estado de California informándole de que Taylor Guitars pronto dejaría de tener autorización para utilizar muchos de los acabados comunes en la industria. Esta prohibición no iba a aplicarse a otros fabricantes de guitarras; solo a los residentes en California. Para una empresa joven con una plantilla en crecimiento, eso tuvo que ser un trago difícil de digerir.
Bob ve la luz
Poco después, Bob asistió a un seminario sobre el uso de luz ultravioleta (UV) para acelerar el curado del acabado. Al volver a la fábrica, declaró: «ese es el camino que vamos a seguir. Haremos lo que sea necesario para desarrollar un acabado más limpio y curado con luz UV». El único problema era que el curado UV aún no existía para objetos tridimensionales como una guitarra, y los fabricantes de acabados no estaban precisamente haciendo cola para ayudar a una pequeña empresa de un sector tan «esotérico». Taylor contrató a un químico para trabajar con Bob y Steve Baldwin, el responsable del departamento de acabados de Taylor en aquel momento. El objetivo era formular un nuevo acabado y desarrollar un proceso para obtener una masilla para rellenado y un revestimiento superior con la posibilidad de curado UV. Mientras tanto, el diseñador de maquinaria y herramientas de Taylor, Matt Guzzetta, proyectó y construyó a medida un horno UV que permitía curar el acabado en 30 segundos (frente a los 12 días de curado al aire que necesitaba la laca de nitrocelulosa).
El nuevo acabado tenía una base de poliéster y contenía menos disolventes, con lo cual reducía las emisiones nocivas. A diferencia de la laca de nitrocelulosa, el acabado resultante era mucho menos propenso a amarillear con el paso del tiempo y no se craquelaba ante fluctuaciones de temperatura. En 1995, la aplicación de acabados con curado UV pasó a formar parte del proceso de producción. Así fue como Taylor se convirtió en la primera empresa de guitarras que adoptaba los acabados con luz ultravioleta, que demostraron ser más duraderos y además permitían utilizar revestimientos más finos (lo cual también contribuía a mejorar el sonido). El extraordinario recorte del tiempo de secado estimuló la eficiencia de la fabricación y dio como resultado una drástica reducción de las emisiones de COV.
Antes hablábamos de los tres componentes fundamentales de los acabados convencionales: un sólido, un aglutinante y un disolvente o vehículo. Tal como dice Andy Powers, diseñador jefe de Taylor, la tecnología de curado UV cambió las reglas del juego porque básicamente evitaba la necesidad de usar disolventes.
«El acabado UV solo utiliza un sólido y un aglutinante», explica. «Los dos componentes quedan catalizados y cambian de líquido a sólido. No hace falta un disolvente para poder extenderlos sobre una superficie. En otras palabras, el sólido y el aglutinante empiezan siendo extensibles y cambian de estado una vez que se han aplicado sobre la superficie gracias a la luz UV. Por lo tanto, si utilizan menos disolventes es porque en gran parte los eliminan. Esta también es la razón por la que no se pulverizan diez capas con un 85 % de material evaporado: solo pulverizamos dos capas y, excepto la pequeña parte que se pierde durante el lijado o el pulido, todo el material queda fijado».
Bueno para la empresa. Más seguro para los empleados. Y mejor para el medio ambiente.
«Buffy, la cazaguitarras» y la atracción electrostática
El siguiente gran avance de Taylor fue impulsado por el deseo de aliviar el estrés físico del proceso de pulido manual («buffing» en inglés) y mejorar la homogeneidad entre guitarras. La implementación de la nueva tecnología fue todo un desafío. Los primeros intentos de programar un sistema de pulido robotizado le valieron a la máquina implicada el apodo de «Buffy, la cazaguitarras». Pero, con el tiempo, el equipo le pilló el truco al asunto.
Unos años más tarde, se volvió a aplicar tecnología robotizada, pero en este caso a la pulverización del acabado. El resultado fue una transferencia más eficiente, lo cual redujo tanto el exceso de pulverización como los residuos de material. La eficiencia de la transferencia mejoró aún más con la adopción de la tecnología de atracción electrostática entre el acabado y la guitarra, que utiliza un atomizador giratorio en un entorno climatizado para optimizar la atracción del acabado. Con todo ello, la eficiencia de la transferencia aumentó del 15 % de la pulverización manual a aproximadamente un 85 % con el método robotizado/electrostático. También en ese caso había menos emisiones de COV, menos residuos, más homogeneidad y un ambiente de trabajo más seguro.
Y, para que conste en acta, esas nuevas tecnologías robotizadas no supusieron la pérdida de ningún puesto de trabajo. Todo el equipo se quedó. Solo le hicimos la vida un poco más fácil y redujimos muchísimo la huella medioambiental de la empresa.
Nuestro sistema de pulido robotizado favorece la homogeneidad y elimina la exigencia física del proceso manual.
Y más refinamiento
La llegada de Andy Powers en el 2011 marcó el inicio de una era de desarrollo de acabados aún más finos que fueron posibles gracias a las tecnologías que ya habíamos adoptado. Ese esfuerzo por seguir rompiendo barreras exigía un proceso de fabricación aún más disciplinado: cuanto más fino es el acabado, menos margen de error hay en el taller. Al trabajar con un acabado, no se trata de «acumular» material a través de múltiples capas, sino de ir lijando hasta llegar al nivel deseado. Andy quería un acabado más fino para mejorar el tono, así que el equipo de Chris Carter, el sucesor de Steve Baldwin, se puso manos a la obra para reducir el espesor de nuestro acabado brillante de 6 milésimas de pulgada a solo 3,5 milésimas de pulgada en algunos modelos. Para que nos hagamos una idea, una hoja de papel de oficina tiene un grosor de 3 milésimas de pulgada. Y, por si alguien se lo está preguntando: sí, podemos medir con precisión el espesor del acabado de una guitarra con un calibrador ultrasónico.
Acabados a base de agua
En el 2019, Taylor empezó a usar un acabado precatalizado a base de agua en algunos modelos. Estos acabados ofrecen una fuerte adhesión tras la aplicación y generan incluso menos COV dañinos. Es más: no solo son más ecológicos, sino que muchos guitarristas los encuentran más agradables al tacto.
El origen del uso de acabados a base de agua en Taylor Guitars es consecuencia de un trayecto en coche y una pandemia mundial. Un día, Bob Taylor llevaba a Chris Carter en su nuevo Tesla. Durante el viaje, los dos iban elogiando el salpicadero de madera. Chris conjeturó que había sido tratado con un acabado a base de agua y prometió investigar el tema. Poco después, empezó a experimentar y a hacer pruebas con cajas de guitarra desechables. Al cabo de unos seis meses, ya estaba seguro de que había encontrado un acabado satinado alternativo que era más seguro y más fácil de trabajar que el barniz de conversión. Chris le habló de ello a Andy Powers, que unas semanas después empezó a utilizarlo en un prototipo aún inédito en el que estaba trabajando. Los resultados de las pruebas fueron excelentes.
Pero, el 19 de marzo del 2020, la pandemia de COVID-19 desencadenó el cierre inesperado de la fábrica, seguido unos días después por la clausura de la planta de Tecate. Igual que al resto del mundo, nos dijeron que nos fuéramos a casa y allí nos quedáramos. Y sucedió algo curioso: la gente se aburría, y muchas personas desempolvaron sus viejas guitarras o decidieron comprarse una nueva.
Ese fue el contexto en el que nació nuestra serie American Dream, una reacción pragmática a la realidad de la vuelta al trabajo de construcción de guitarras durante una pandemia que había interrumpido las cadenas de suministro y las había hecho impredecibles. Para resumir, Bob y Andy echaron un vistazo rápido a nuestro inventario de madera disponible y se propusieron «cocinar con lo que había en la despensa». La idea era construir una guitarra utilitaria de madera maciza y con el varetaje V-Class de Taylor que pudiera producirse íntegramente en los Estados Unidos y venderse a un precio más asequible. Las guitarras American Dream han tenido un éxito enorme, pero no se ha hablado tanto del gran salto que en aquel momento dio Taylor con los acabados a base de agua.
Cuando se permitió que pequeños equipos esenciales regresaran a la fábrica bajo las nuevas normas de seguridad y distancia social, todos estábamos bajo presión. Teníamos que sobrevivir como empresa y nos veíamos obligados a hacer más con menos. En aquellas circunstancias, un proceso de acabado más rápido y menos laborioso era lo que necesitábamos. Y ahí estaban Chris y su equipo con un nuevo acabado a base de agua que se utilizó en varios de los nuevos modelos American Dream y también para la guitarra GT Urban Ash. Ese acabado nos convenció inmediatamente, ya que es más duradero que un barniz de conversión y el proceso de aplicación también es más ecológico.
Menos es más
En anteriores artículos de Wood&Steel he comentado que el aspecto más prioritario, importante y que muchas veces se pasa por alto de la sostenibilidad es la eficiencia. Algo tan simple como «usar menos de todo». Y las constantes innovaciones de Taylor en el acabado para guitarras son un buen ejemplo de ello. Las regulaciones ambientales de California, cada vez más estrictas, espolearon el desarrollo de un acabado de poliéster curado con UV que resultaba más limpio y fino. Nuestra iniciativa para reducir el estrés físico del proceso de pulido manual (y para hacerlo más homogéneo) condujo a una nueva era de robotización del pulido y la pulverización que mejoró la eficiencia de la transferencia. Un trayecto en el Tesla de Bob seguido de una pandemia aceleró la adopción de acabados a base de agua. Todas estas circunstancias desembocaron en un uso de materiales más seguros y en menor cantidad. Mejor para Taylor Guitars. Mejor para la gente que trabaja con nosotros. Mejor para el medio ambiente. Y mejor para los guitarristas.