I recently acquired an amazing new addition to complement my already amazing XXXV-GS-C. I came across a custom 12-fret Grand Concert from last year with V-Class bracing, slotted headstock, sinker redwood top, and “Queen’s” walnut back/sides, and I just could not resist! Thank you for these two incredible instruments, which I will cherish for years to come.
The story of the Queen’s walnut tree is fun and fascinating in itself, but I have never had a walnut guitar before, nor one with such figuring, and I noticed something that got me thinking. On the outer lower bout, there is small area where I can actually feel very subtle ridges that correlated to the figuring, almost like waves. To the naked eye, there is nothing to be felt and is smooth as can be with a satin finish. Then I noticed that for the most part the figuring occurs at 90 degrees to the grain. My thought is that at this location, with the side wood being shaped around the curve of the bout, I can feel the figuring because of different densities in the walnut. Is my hunch correct?
Also, I am sure you have addressed a similar question in the past, but can you dumb down the biology and physics of figuring in layman’s terms? How much is dependent on wood species and tree development? Or is it just how the wood is cut? Read Answer
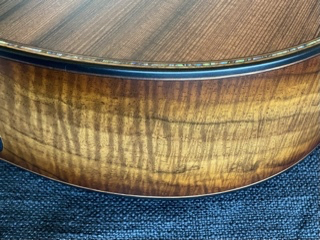
Brian, I’ll answer this in writing, but I’ll also make a video. The flamed figure you see in your beautiful walnut is a result how the tree grew. It’s genetic, even though it can be produced from stress such as in the fork of a trunk or the intersection of a big branch. But your guitar wood came from a tree trunk that grew this way regardless of any stress. To understand how the grain is oriented inside this type of tree, imagine a length of solid plastic drain pipe. And beside it, imagine a length of plastic flex pipe. Now imagine standing them on end, side by side, to imitate two tree trunks. The solid pipe is what a normal, straight-grained tree looks like, and the flex pipe represents a tree that has grown so that it will have flamed figure when cut into boards.
Similarly, imagine plucking a length of long hair from the head of a person and holding it up to notice that it hangs straight, and then imagine plucking a long length of highly curly hair from another person and holding them side by side. One is a representation of a long fiber of wood from the straight-pipe tree, and the other from the flex-pipe tree. Can you see this in your mind? When we cut a board along the length of the flex-pipe tree, the individual fibers run in and out of the surface of the wood, in the same way that the curly strand of hair would run in and out of a straight line. This causes light reflection that displays what you see on your guitar. With people, we accept straight hair and curly hair as being a result of your genetics. Yet with wood, people are trying to figure it out. But in the simplest way, it’s just like curly hair.
I have never owned a nice guitar before. I just bought my first Taylor guitar, the Builder’s Edition 324ce, and I’m thrilled with it. Now I’m learning how to take care of it and make sure it’s playing its best. Do I need to lubricate the nut? I see that a lot of people use a lead pencil. However, I’m not really keen on drawing on my nice new guitar. Do I need to do this? And is there any circumstance where it would be necessary? My guitar does seem to fall out of tune throughout the week. However, I’m not sure if lubricating the nut would even help. Read Answer
Andrew, thanks for checking. I don’t think you need to lubricate your nut. Yes, pencil graphite is a good dry lubricant and not harmful at all, but the only reason you’d need it would be if your strings are binding in the slot, and I doubt that’s the case. When tuning your guitar, it’s always more stable to lower the string and tune up to the note. Then, pull a little bit on the string. If the tension loosens a bit, tune up that little bit to arrive at the correct note on your tuner and you’ll have pretty stable tuning. Your guitar is new, and over time the wood will settle in more and the guitar will stay in tune longer.
Recently, a group of friends and I were jamming. Our lead guy had a 14-year-old 910ce, I had an eight-year-old 814ce, the third player had a four-year-old 714ce, and the fourth guy had a brand-new 814ce. As we played, each time the new 814ce guy came in for his part, his guitar roared past the other three. The volume was so much higher. All the players noticed it. All the guitars sounded great together, but the new one really boomed. We were all using Elixir strings, and the newer guitar had the strings that came with it. Any idea why the big volume difference? Read Answer
Ed, our readers will think you’re a plant by the company, but I assure them all you’re not! This is likely the result of V-Class bracing in the new 814ce. It’s got more volume and more sustain due to its design. It is very stiff and strong along the direction of the strings, which increases sustain as well as stability. In addition, it’s more flexible from side to side, which gives it volume. This is the brilliance of this design. It’s pleasing to hear that you can tell the difference. You describe it in quite strong terms, while to me it’s subtler than that, but I love hearing about a guitar roaring past the others!
I love my 814ce. It just gets better and better! My two daughters love their Taylors as well. I was wondering, considering all of the innovations Taylor has introduced, is there any new feature or modification your team has considered that seemed to be the next “Taylor Neck” or V-Class bracing-esque innovation but never made it into production? Read Answer
Stephen, we do have some next-level things that make the guitar much better. Unfortunately, I can’t talk about them — I hope you can understand. One in particular is very impressive, it’s just that we cannot find a way to make it quite yet. When we do, it will allow our guitars to take another step forward. There are others too, but being in the R&D stage I have to stay quiet, which is hard for me.
Believe it or not, we’ve been drying and seasoning wood for decades, developing recipes that help us make the best guitars possible. And we’re still working on improving that process each week as if we are beginners and barely know anything. This is the kind of stuff that makes coming to work so rewarding. How’s all that for a non-answer? I wish I could go down the list and identify what we hope to achieve and have already solved but haven’t been able to implement yet.
I recently purchased a Taylor K24ce with V-Class bracing without having a chance to play it in person. In my experience, that is always a risk, but particularly with an all-koa guitar. I have owned and played multiple koa guitars in the past and found the tone to be inconsistent; when you get good koa tone, it is glorious, but when you get a bad one, it sounds harsh and thin. I expressed this concern to the salesperson at Wildwood Guitars when I told him of my interest in the K24ce, and he told me that the koa wood used by Taylor Guitars more recently is extremely consistent and sounds good right out of the case as opposed to needing much time to open up. I was a bit skeptical but decided to give it a shot, and when the guitar arrived, I was amazed at the tone. I had all kinds of preconceived notions about koa as a tonewood, and all of them were proven false when I played it for the first time and for the subsequent hours of time I have spent with it. For example, I bought this for use solely as a fingerstyle instrument, as I find koa guitars to be a bit too bright when strummed, but when I strum this guitar, it sounds as good as any dreadnought I have that is used primarily as a strumming instrument. Also, I expected to hear tone potential, but with the notion that it would take years of playing to bring out that koa tone I was hoping for. Yet when I played it out of the case, it already had the tone I was hoping for. So, this guitar has exceeded all of my expectations of a koa guitar, and is surprisingly the most versatile instrument I own. So, my question is, what is Taylor doing with its koa lines that seems to have addressed a lot of my concerns? I suspect the V-Class bracing has something to do with this, but is there anything else Taylor has done recently to indeed produce a consistent and opened-up tone? Read Answer
Lenny, that’s quite a review, thank you so much. The aw-shucks part of me wants to downplay and say, “Well, the guitar fit the tone you were looking for, so of course you think it’s amazing. Maybe someone else would feel differently.” But I’m not going to say that. The hype part of me might want to take advantage and say, “We at Taylor have developed our own koa supply and have control of it from the tree in the forest to the guitar you opened the day it arrived, so we can guarantee an incredible guitar every time.” I’m not going to say that either, even though there is truth to both ideas. Here’s the thing: We make so many koa guitars, and we do control it all the way. As you know, we own a koa company in Hawaii in partnership with tonewood supplier Pacific Rim Tonewoods. Nobody cuts and processes wood for guitars like they do. In addition, we have special drying schedules, as I mentioned in a previous question, whereby we can relax our wood more than we’ve ever been able to in the past. It’s quite arduous and costly, but we feel it’s worth it. Hearing your comments help cement that feeling. And then, on top of that, “LONG LIVE V-CLASS!” It’s really a nice way to make a guitar. Especially a koa guitar that needs to be both stiff and flexible.
We know how excellent pre-war, X-braced guitars sound. How do you think V-Class Taylors will sound decades from now? Read Answer
Good question, Carlos. They’ll sound incredible. They’ll continue to develop into better and better sounding guitars as the wood ages and the vibrations of playing loosen them up. We could go down a rabbit hole where I’d confuse even myself, but older guitars sound better than newer guitars. Pretty much always.
I was delighted to read about Taylor’s ongoing efforts to utilize urban trees from around the world. I purchased my Taylor 610 in the late ’80s when the guitar was still being made with German maple, which I believe is hard to find now in high quality. On a trip to Scotland about 15 years ago, we met a family from Germany that had just built and installed a new church organ in Glasgow. They told us [the project] had been in the works for over 10 years and used wood purchased by the family more than 30 years earlier. They have been building organs for over 400 years and were headed to Asia to purchase wood for orders they expected to deliver in 30 years. They were not optimistic that they could find woods of the quality for which their family was known and felt the wood quality challenge might soon become the end of the business.
I now live in Florida and have a few small pieces of land that I would like to plant trees on that might someday be used to create great musical instruments. Do you have any suggestions on what to plant or how best to start and space trees so small landowners like us might improve the future musical instrument-grade wood stock? Read Answer
Oh my gosh, John, I cannot answer how to plant trees in an Ask Bob column. But I lift a glass high and toast that you want to do this. This is my dream that more and more people like you would do this. Thank you! There are some interesting trees that could grow there, like Sisso rosewood, which, if grown straight and tall as can be, with round trunks, would make a nice wood source for guitars. The Shamel ash we get from Los Angeles city streets also will grow in Florida because it’s a tropical tree. You can google tropical ash or Shamel ash for species. Trees that are good for lumber need to be grown straight and tall as can be, and hopefully without lost dog signs nailed to them. I really do hope to be able to supply more information in coming years to people who want to plant trees on their property. The two species I mentioned are something you could look around to find in a nursery. That’s the next problem — finding those trees. Both species have invasive roots, so they need to be planted where that’s not a problem. Do walnut trees grow there? They’re American and make nice wood.
Your company’s programs and efforts in the area of sustainability are truly impressive. The introduction of the Urban Ash model is a great part of that story, and it makes me wonder if you have thought about making a “hundred-mile guitar,” where absolutely all of the parts and materials are sourced from within 100 miles of the factory. I’m sure it would force some limitations. But it would be a grand experiment in efficient and sustainable manufacturing, and I think it might be interesting to some of your customers. Read Answer
Yes, that could be quite interesting, Mark. I’m glad our factory is in a place where we at least have had trees planted years ago. We could draw on those rather than native species. If it were a challenge to use only wood from here, I’d pick Shamel ash for the sides, back, top and neck. I’d pick red iron bark eucalyptus for the fingerboard and bridge. I’d have to make braces, and again I might choose the ash. We have some pine trees that grow in our mountains that might make a good top and bracing if we got one from high elevation. But it’s slim pickings here for a guitar maker, which only points out what planting can do, since it’s given us a veritable garden of wood to choose from here, now three-quarters of a century after people planted non-indigenous trees here, many of which have reached end of life.
Bob, a friend of mine who is a retired guitar tech happened to mention that Taylor’s use of what he called “glued-on headstocks” results in a loss of low-frequency (bass) response. In addition, he said the joint (I believe it’s a scarf joint) creates a point at which the neck could break in the event of an accident.
He also believes that the string load on smaller-bodied 12-strings can cause the need for repairs down the road. This concerns me since I’m considering getting a 352ce or 362ce. Could you shed some light on these contentions? Read Answer
Well, Bob, I don’t want to pick a fight, but we do know a lot about how to make a guitar, or millions of them, shipped all over the world, many that have held up for half a century. All classical guitars, no matter what the price, have “glued-on headstocks.” All Taylors do as well. In fact, everything on the guitar except our neck itself is glued on. I’ve got no fear of glue. I guess you can hear the bass for yourself. As to the strength, they’re not weaker, they’re stronger than one piece. The grain on a one-piece neck runs right through the angle, making a very breakable spot. This is where guitar necks break. We don’t really experience broken headstocks on our guitars since we started making scarfed joints. Our joint is also quite complex and hard to make. Look at it from the back and notice how it comes down to the nut in a “ducktail” fashion. It’s quite thin there and bends like a saxophone reed, allowing it to flex and spring rather than break. It’s really quite good. It also takes some serious tooling to manufacture it exactly right, which was a huge investment to accomplish. As far as the small-bodied 12-string goes, it’s not going to suffer any maladies. All I can do is refute the claims of a retired guitar tech. I’m happy to do that, as I know more about it. And remember, we give you a lifetime warranty when you buy our guitars. That might be worth something.