Here at Taylor Guitars, we like to say that sustainability is a journey, not a destination. It’s a mindset that keeps us from getting complacent. Accordingly, we’re looking at a range of issues — beyond the obvious topic of wood consumption — including energy use, plastics and single-use disposable products, and even the T-shirts we sell, in order to find ways to act more responsibly, without compromising the standards that built the company. We’re far from perfect, but we’re making progress. Like I said, it’s a journey.
Part of being a responsible company is transparency. So, in this article, I wanted to focus on guitar finishes and explain where we’ve been, where we are, and where we’re trying to go.
I should start by acknowledging that among guitar enthusiasts, finish can be a surprisingly emotional topic. Trust me, if you want to ignite a debate among luthiers and opinionated players, walk into a room and start talking about finishes. This is due in part to the long history of finishes for string instruments, but also to the range of opinions about how different finishes impact a guitar’s sound, feel and look.
More Than Just a Coating
Guitars that reach the finish department in our factory in El Cajon, California, transition through a series of processes, including sanding, staining, grain-filling and topcoat finish application. Think of a good finish not merely as a protective coating, but as a refined system, often incorporating different materials and technologies, applied in a succession of integrated layers that each serve a specific function. For example, grain filler penetrates and stabilizes the wood, especially open-pore species like mahogany. Another finish layer will protect the wood and provide just the right amount of damping. (For more on finish and damping, see our sidebar.) Another layer of a finish system is the topcoat, typically applied with the aesthetic appearance in mind, sometimes highlighting grain patterns and enhancing color consistency.
Finish Materials Through the Years
Throughout the centuries, many different materials have been used to finish wooden musical instruments, such as oils (e.g. linseed or tung), waxes, shellac (a resin secreted by the lac bug of India and Thailand), varnishes and various lacquers. At a fundamental level, most finishes have three components: a solid (such as resin), a binder (to help the finish adhere to the wood and solids to each other), and a vehicle (e.g., solvent, oil) that helps dissolve the resin to make it spreadable.
To better understand the evolution of guitar finishes, including our own, it’s helpful to look back at the instruments that influenced their development, such as the oud and lute. Centuries ago, the wood on these instruments was protected using locally available natural ingredients like glair, a concoction of sugar (used as a resin for durability), egg white (a binding agent), and honey (the application vehicle, which also gives the surface a degree of flexibility). Sometimes hardened sap, perhaps from an acacia tree, might have been incorporated.
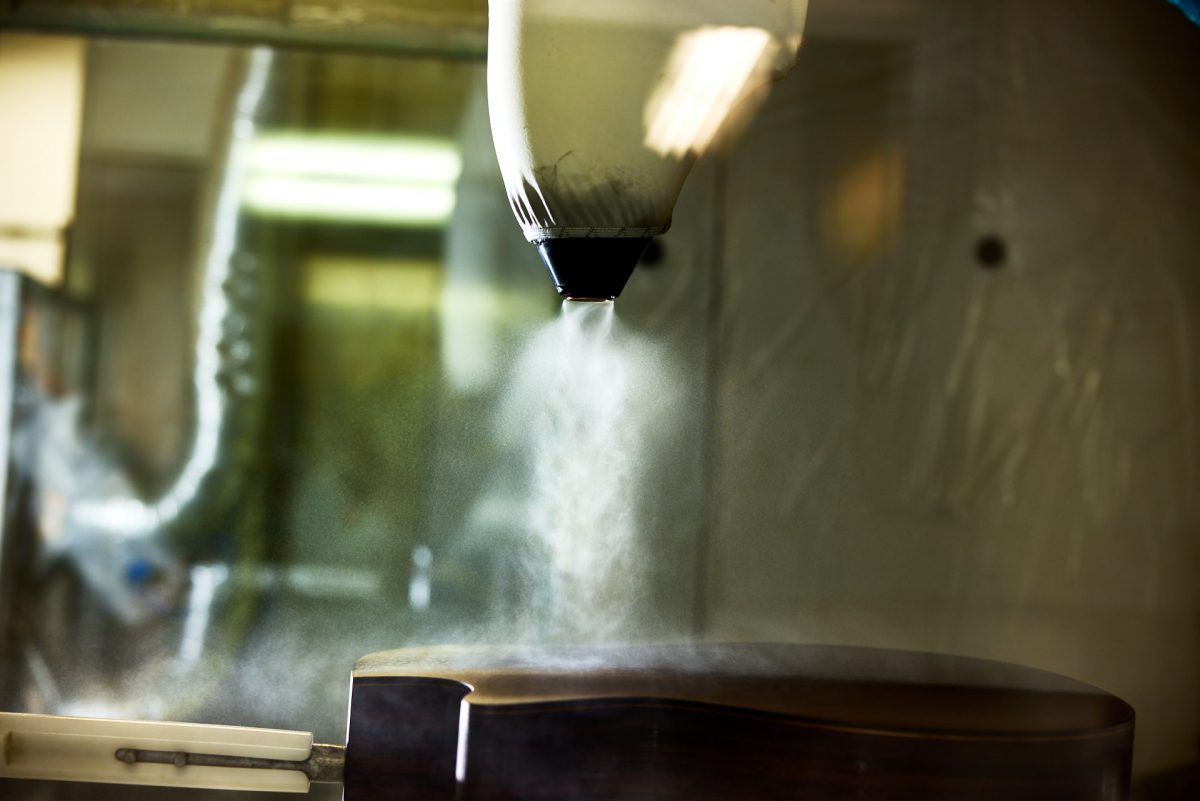
A Word on Finish Thickness and Damping
There is a definite correlation between finish thickness and damping. For example, here at Taylor, we’ve talked about this alongside the introduction of some of our thinner, tone-enhancing finishes over the years. Too much finish will overly restrict the guitar’s resonance and musicality. But what you might not realize is that too little finish — or no finish — won’t provide enough damping control, which can lead to clashing overtones and sometimes a shrill acoustic voice. So damping is not an inherently bad thing when it comes to sound.
French Polishing
Wooden instrument finishes really came of age starting in the 1600s, with the violin setting the tone (both literally and figuratively) for the instrument finishes that followed. A high-gloss wood finishing technique called French polishing migrated from the violin world to classical and parlor guitars in the 1800s and 1900s. The technique took its name from its extensive use in France by Victorian-era furniture makers. The highly labor-intensive process involves applying many thin coats of natural shellac, secreted by the lac bug, dissolved in denatured alcohol, and rubbed in with an oil-lubricated pad. Because alcohol evaporates quickly, the drying time between each application is very short. The downside is that each coating is so thin that the process demands the application of hundreds of coats (no exaggeration) to achieve the highly polished surface that people love.
Nitrocellulose Lacquer
In 1921, the chemical company Dupont invented nitrocellulose lacquer for the automotive industry. The first modern, synthetic finish, it was durable, dried to the touch in minutes, and could be applied with a spray gun, making it perfect for the dawn of mass production. The process was soon adopted by woodworkers, including guitar makers.
Nitrocellulose lacquer wasn’t without its problems. For one thing, with conventional spraying methods, the transfer efficiency — the amount of finish that actually attracts to the target rather than just going into the air — was only about 10 percent. On a wooden guitar, the solvents required to apply it required upwards of two weeks to air cure. In fact, that solvent off-gassing process can continue for months and even years, making the finish thinner but denser. Over time, nitrocellulose finishes are also prone to yellowing, and in the face of dramatic temperature fluctuation, can produce small hairline cracks, commonly referred to as “finish checking.” For some vintage guitar collectors, such characteristics enhance the aesthetic charm.
Solvents and VOCs
What was little understood in the early days of nitrocellulose lacquer was that the solvents used were not without problems. Especially if applied with a spray gun in an open factory setting, nitro released significant levels of volatile organic compounds (VOCs), many of which are dangerous to both human health and the environment. Yes, VOCs are ubiquitous and also occur naturally. Open a bottle of wine and VOCs are released. It’s just a gas, and some gasses are harmless, while others are not. But the VOCs released when nitrocellulose lacquer is applied with a spray gun can be poisonous and cause adverse human health effects, including short-term eye, nose and throat irritation, shortness of breath, headaches, nausea, dizziness and skin problems. Longer-term effects can include damage to the lungs, liver, kidneys or central nervous system. Nitrocellulose lacquer finishes are still commonly used today in several industries, including guitar making, albeit in a far safer application environment, in order to protect workers.
Taylor’s Finish Evolution
Over the years, scientific advancements in the world of plastics and polymers produced new forms of finishes, and several, such as conversion varnish, urethanes, polyurethane, polyester and acrylic, have been adopted by the guitar industry. All are simply different resins based on evolving science, and each releases various levels of VOCs. When Taylor Guitars first set up shop in 1974, the fledgling company adopted a variety of finishes and application methods common to the industry at the time, from nitrocellulose lacquer to conversion varnishes, and later, polyurethane. Each brought its own inherent environmental issues, with the common denominator of a lengthy curing time.
Around 1985, Taylor completely phased out nitrocellulose lacquer finishes. Over the years, Taylor’s finish team has continued to radically transform our processes, progressing from a highly manual, labor-intensive approach to a sophisticated, technology-driven science.
Crisis is the Mother of Invention
Bob Taylor has always been a self-driven innovator, but sometimes the motivation can come from external sources. Like the day in 1991 when Bob received a letter from the State of California informing him that Taylor Guitars would soon no longer be permitted to use many of the finishes common to the industry. Other guitar makers could use them, just not those based in California. For a young company with a growing workforce, that must have been a difficult pill to swallow.
Bob Sees the Light
Not long afterward, Bob attended a seminar on using ultraviolet (UV) light to accelerate the finish curing process. He returned to the factory and declared, “This is where we’re going. I want to do whatever it takes for us to develop cleaner, UV-curable finish for our guitars.” The only problem was that UV curing didn’t yet exist for three-dimensional objects like a guitar, and finish manufacturers weren’t exactly lining up to help a small company in an obscure sector. So, we hired a chemist who worked with Bob and Taylor’s finish department manager at the time, Steve Baldwin, to formulate a new finish and develop a process of getting a UV-curable top coat and paste filler. Meanwhile, Taylor machine and tool designer Matt Guzzetta designed and built a custom UV curing oven, which enabled the finish to be cured in 30 seconds — compared to the 12-day air curing time required with nitrocellulose lacquer.
The new finish was polyester-based, contained fewer solvents, and thus reduced harmful air emissions. Unlike nitrocellulose lacquer, the resulting finish was much less likely to yellow with age and didn’t fall prey to checking with temperature fluctuation. By 1995, UV-curable finish application became part of the production process, making Taylor the first guitar company to adopt ultraviolet finishes. They proved more durable and enabled a thinner coating to be applied, which yielded tonal benefits too. The extreme reduction in drying time drove manufacturing efficiency and resulted in a dramatic reduction of off-gassed VOCs.
Remember those three fundamental components of conventional finishes mentioned earlier: a solid, a binder and a solvent or vehicle? As Taylor master builder Andy Powers explains, UV-cured finish was a game changer because the technology essentially eliminated the need to use solvents.
“The UV finish has a solid and a binder only,” he says. “The two components are catalyzed and shift from liquid to solid. They don’t use a solvent to make them spreadable. In other words, the solid and binder start out as spreadable, then change state once they are spread out on the surface with the help of UV light. So the way they use less solvents is by largely eliminating them. This is also the reason why we don’t spray ten coats, with 85 percent evaporating; we spray two, with nearly everything remaining except the little bit that gets sanded or polished away.”
Good for the company. Safer for employees. Better for the environment.
Buffy the Guitar Slayer and Electrostatic Attraction
The next big advancement at Taylor was driven by a desire to relieve the physical stress of the manual buffing process, and to improve the consistency from guitar to guitar. Implementing the new technology was a challenge, and early efforts to program a robotic buffing system earned the machine the nickname “Buffy the Guitar Slayer,” but in time the team figured it out.
Several years later, robotic technology was applied again, this time to finish spraying, resulting in improved transfer efficiency, which in turn meant less over-spraying and material waste. The transfer efficiency was further improved with the adoption of electrostatic attraction technology between the finish and the guitar, which incorporates a rotary atomizer and a climate-controlled environment to optimize finish attraction. In the end, the transfer efficiency was increased from about 15 percent via manual spraying to about 85 percent with the robotic/electrostatic method. Again, fewer VOCs, less waste, more consistency and a safer working environment.
And for the record, these new robotic technologies did not replace any jobs. We kept everybody. We just made their lives a little easier and greatly reduced the company’s environmental footprint.
Our robotic buffing system enables greater consistency and eliminates the physically demanding workload of buffing manually.
Getting Even Thinner
The arrival of Andy Powers in 2011 ushered in an era of developing even thinner finishes at Taylor (made possible by the technologies we had embraced). These envelope-pushing efforts required an even more disciplined manufacturing process, as a thinner finish reduces your margin for error on the shop floor. With any finish, you don’t “build up” via multiple coatings, but instead sand down to hit your desired level. For tone-enhancing purposes, Andy wanted a thinner finish, and Steve Baldwin’s successor, Chris Carter, and his team helped reduce our gloss finish thickness from 6 mils (.006 inch) to as low as a 3.5 mils (.0035 inch) on some models. To give you some perspective, a sheet of office paper is 3 mils (.003 inch) thick. (And in case you were wondering, we can accurately measure finish thickness on a guitar with an ultrasonic gauge.)
Water-Based Finish
In 2019, Taylor began using a precatalyzed water-based finish on select models. It offers strong adhesion upon application and produces even fewer hazardous VOCs. In addition to being more environmentally friendly, many players say water-based finishes feel better to the touch.
The origins of water-based finishes at Taylor Guitars stem from both a serendipitous car ride and a global pandemic. One day Bob Taylor was driving Chris Carter in his new Tesla, and the two were admiring the wooden dashboard. Chris assumed it was treated with a water-based finish and promised to look into it. Soon thereafter, Chris started running experiments and conducting tests on scrap guitar bodies. After about six months, he was confident that we had an alternative satin finish that was safer and easier to use than conversion varnish. Chris mentioned it to Andy Powers, and a few weeks later Andy began using it on a still unreleased prototype he was working on. The tests yielded great results.
Then on March 19, 2020, the COVID-19 pandemic triggered the unexpected shutdown of the factory, followed a few days later by the closure of Tecate factory. We were all told to just go home, as were people around the globe. And a funny thing happened. People got bored. And a lot of them dusted off their old guitars or decided to buy a new one.
Our American Dream Series was born at this time, a pragmatic reaction to the realities of returning to work and building guitars during a pandemic, when supply chains were disrupted and unpredictable. To summarize, after a quick look at our existing wood inventory, Bob and Andy started talking about “cooking with what’s in the pantry” and building a utilitarian guitar, with solid-wood construction and Taylor’s V-Class bracing, but also something that could be produced in the U.S. and sold more affordably. The resulting American Dream guitars have been a big success, but less discussed was the leap forward Taylor made at that time with water-based finishes.
When small skeletal crews were allowed to return to the factory under new safety and social distancing norms, they were under pressure. We needed to stay alive as a company, and we needed to do more with less. A faster, less labor-intensive finishing process would help, and Chris and his team were ready with a new water-based finish that was ultimately used on several of the new American Dream models, and for the new GT Urban Ash guitar too. It was an immediate success, considered more durable than a conversion varnish. And the application process was also more environmentally friendly.
Less Is More
I’ve mentioned in previous Wood&Steel articles that the first, most important and often most overlooked aspect of sustainability is efficiency. The simple act of using less. And Taylor’s continuing innovations with guitar finish are a good case in point. California’s ever-increasing environmental regulations spurred our development of cleaner, thinner, UV-cured polyester finish. An initiative to relieve the physical stress of the manual buffing process (and increase consistency) led to the an era of robotic buffing and spraying, resulting in improved transfer efficiency. A drive in Bob’s Tesla followed by a pandemic expedited our adoption of water-based finishes. All result in using safer materials, and less of them. Better for Taylor Guitars. Better for the people that work here. Better for the environment. And better for players.