Over nearly five decades of Taylor history, being unencumbered by tradition has repeatedly proved to be one of our greatest strengths. It’s given us the creative freedom to continually explore new ideas and push the parameters of guitar-making in exciting new directions.
One ongoing area of exploration has been our use of tonewoods. Some of this has been fueled by our desire to discover new sonic flavors. And some of it has been guided by the modern-day realities of sourcing wood and the need to respect what the world’s forests can provide.
Over the last decade in particular, the environmental stewardship projects we’ve launched have strongly guided the wood sourcing choices we’ve made. You probably know of our work with ebony in Cameroon starting in 2011, including our adoption of long-overlooked variegated ebony for our fingerboards. In 2020, we introduced our first models featuring Shamel ash from end-of-life trees in need of removal from communities in California. And a few months ago, we debuted our koa 700 Series, featuring a new grade of Hawaiian koa that we discovered in the course of our forest restoration efforts in Hawaii.
Our guitar line is a carefully curated and always evolving musical ecosystem.
The truth is that our guitar line is a carefully curated and always evolving musical ecosystem. Despite our growth into a larger guitar company, we’ve managed to balance the need to create a stable, ethical supply chain with the ability to be nimble in response to the ever-changing world around us.
What Makes Good Guitar Wood?
There are many considerations that go into deciding which woods we choose to showcase within our guitar line, especially when we consider a new species that isn’t already associated with musical instruments. First and foremost, does it have physical characteristics that translate well into musical sounds? Equally important, is the wood workable — in other words, can it be cut, dried, sanded, bent, glued and transformed into a guitar without warping, cracking or causing other problems during production or after completion? Can it be ethically and economically sourced? Can we find a consistent level of quality? Is there a sufficient quantity to meet our supply needs for a foreseeable period of time? How long will it take to get it from a supplier? Does it bring something unique to our guitar menu? And if it’s a wood that’s essentially a newcomer to the acoustic guitar world, what will it take to captivate players? You get the picture.
Fortunately, as an established company with a strong guitar-making reputation, exacting production standards, a good track record of ethical business, and an enthusiastic customer base (thank you!), we carry a high level of credibility when we champion a new wood.
Also, we have a guitar designer named Andy Powers, who knows how to harness a tonewood’s musical virtues to the fullest.
Diversifying the Line
In this year’s first edition of Wood&Steel (Vol. 102), we talked with Andy about the ongoing evolution of guitar design at Taylor, and about his desire to bring greater musical diversity to our line. One way in which he’s moved the needle is in the nuanced voicing recipes he’s developed to differentiate models, especially after creating our patented V-Class and C-Class bracing platforms, which can be adapted in subtle ways based on the body shape, tonewood pairing and the tone profile he’s trying to elicit from the guitar. Those efforts, together with Andy’s body-style innovations over the last decade — introducing the Grand Orchestra, the Grand Pacific and Grand Theater; reinventing the Grand Symphony; and bringing 12-fret and 12-string configurations to the Grand Concert — have enormously expanded the palette of unique musical personalities in our line.
Part of the process of refining our guitar offerings is to look at our guitar line holistically and evaluate the relationship of one guitar series to the next. For example, with the recent reboot of our 700 Series, we were fortunate to gain access to a healthy supply of beautifully colored and striped Hawaiian koa that Andy felt deserved its own unique voicing and aesthetic treatment in the line, separate from our existing Koa Series. So where would be the right place for it to live? Somewhere, he thought, that would make an all-solid koa guitar a bit more accessible to customers.
In the end, the 700 Series felt like the best position. That would still give us three different aesthetic presentations of our rosewood guitars — the 400, 800 and 900 Series.
Mahogany Migration
Another traditional tonewood, mahogany, has similarly spread to different parts of our line. Within our 300 Series, we added to the sapele and spruce combination we’ve featured for years with mahogany-top models. For a time, we paired Tasmanian blackwood back and sides with mahogany tops. More recently, we decided to replace blackwood with mahogany and give players several all-mahogany model options within the series. That made Andy think more about our use of mahogany and the evolution of our 500 Series, which has featured mahogany for decades. With all-mahogany guitars available in the 300 Series, what might the 500 Series become?
Meanwhile, there was another urban wood — red ironbark — that Andy had been working with for several years and planning to introduce within the line when the time was right. This seemed like a golden opportunity.
Urban Wood Revisited
Before we get into red ironbark, we should recap our urban wood initiative. In early 2020, we released four new models under the banner of our Builder’s Edition collection. One of them, the Builder’s Edition 324ce, featured back and sides of Shamel, or evergreen, ash, which we chose to call Urban Ash to draw attention to the unique origin story of the wood.
This California-grown ash was exciting to Andy not only for its intrinsic characteristics, but because it marked the beginning of a promising new urban sourcing initiative in collaboration with West Coast Arborists, Inc. (WCA), a sophisticated tree management operation.
As we detailed in that issue of Wood&Steel, WCA provides an array of tree services to hundreds of municipalities and public agencies across California and parts of Arizona. These planned and managed tree programs create the important green canopies for cities and suburbs, including landscaping in parks and other public spaces, and along neighborhood streets and highways. As part of a contract agreement with individual municipalities, WCA plants, cares for and eventually removes these trees, and more than 10 million tree sites are inventoried in WCA’s proprietary database.
Our interest in exploring the viability of urban wood was first spurred by Bob Taylor’s practical curiosity about what happens to the wood from these end-of-life trees, and whether these trees could be utilized to create additional value for communities. As we’ve shared in other stories, we reached out to our local arborist, who happened to be WCA.
Our Director of Natural Resource Sustainability, Scott Paul, led the charge, coordinating a field trip with a Taylor group including Bob and Andy to WCA’s headquarters in Anaheim to meet with their team. It turned out that WCA also had been looking for ways to create greater value from these the end-of-life trees they had removed — especially in the wake of rising disposal costs — and had launched an urban wood recycling program turned supply business called Street Tree Revival, which cuts lumber and produces live-edge slab tables and other wood products. They also had set up a sort yard in nearby Ontario with logs arranged and color-coded by species.
Because many of these species either weren’t commercially used or weren’t established music instrument woods, Andy went “taste testing with a chain saw,” cutting samples from certain species that seemed worthy of investigating further.
“It was like being a chef walking down the aisle of a farmer’s market and seeing vegetables or fruits they haven’t encountered before,” Andy says. “You start thinking, how can I work with this to bring out its best flavors?”
Andy brought a healthy variety of wood samples back to the factory for some testing. He also narrowed the list of species based on practical considerations, focusing on what he considered the top 10 contenders.
“Many tree species simply don’t have the practical characteristics that allow them to be used for woodworking.”
Andy Powers
“From a supply standpoint, we wanted to know which trees were most abundant,” he says. “Then I looked for ones with the right kind of structure, height, diameter to supply boards, and working characteristics. A few of these species checked those boxes, Shamel ash being one of them. You could dry it, saw it, glue it, sand it, finish it. It might sound odd to say, but many tree species simply don’t have those practical characteristics that allow them to be used for woodworking. And then beyond those simplistic criteria, the wood has to yield a great sound. It’s a tough test for a tree to pass.”
Being able to properly dry wood, Andy says, is a critical consideration.
“The reason we spend so much attention on whether we can dry the wood is that this directly translates into whether that guitar will be stable over its lifetime,” he explains. “Essentially, if you can’t dry a piece of wood without it cracking, warping, breaking or distorting itself, you’ll have a difficult time making something consistent and reliable from it. Somewhere down the road, poorly behaved wood will cause problems.”
With Shamel ash, Andy had a strong feeling it would make a good tonewood due to familiarity with other ash species for guitars.
“I’ve worked with a lot of ashes — from northern hard ash to lightweight swamp ash,” he says. “In this case, looking at the type of grain structure of this ash, I had a reasonable expectation that it was going to work well, and it ended up working even better than we expected. That wood had such great characteristics and was so similar to woods we knew well, we felt it made sense to launch our first urban wood guitar with that.”
[Ed. note: Elsewhere in this issue, we unveil two all-Urban Ash limited-edition models, the 424ce LTD and 224ce-UA DLX LTD.]
A New Tonewood Star Is Born
A surprising discovery, which would prove to be a serendipitous find, was a wood known as red ironbark (Eucalyptus sideroxylon).
“Red ironbark was an unusual one,” Andy says. “Technically it’s from the eucalyptus family, but it doesn’t behave like most eucalyptus, many of which tend to twist and move in unpredictable ways. Even more surprising, this red ironbark is ultra-hard and dense, as if it were some type of tropical rosewood-family wood. In fact, it’s one of the few woods that will actually sink in water. It’s like ebony.”
As Andy explored its mechanical characteristics in more detail, he was pleasantly surprised by its workability — it could be dried consistently without complications.
“Usually, denser woods are hard to dry and prone to distortion, which needs to be carefully controlled to yield a stable guitar part — like ebony,” he explains. “With red ironbark, we were surprised to find we could dry it consistently well the way we might dry East Indian rosewood. This ironbark has similar characteristics in that regard. It’s very stable.
Another stereotype of woods this hard — and there are only a few such woods, Andy notes — is they have oily content that makes gluing difficult. Once again, the red ironbark proved to be an exception.
“On top of all of this, it has one of the smoothest and most uniform textures of any dense wood I’ve ever seen,” he says.
With its hardness, density and smoothness, Andy initially considered it for fretboards and bridges, but with its rosy and golden-brown hues, he opted against it for the time being. But he suspected it would work really well as a back and side wood. It turned out he was right.
Getting to Know Red Ironbark
Red ironbark, or its more complete name, red ironbark eucalyptus (Eucalyptus sideroxylon), is one of more than 700 eucalyptus species found around the world. The history of eucalyptus species in California traces back to the 1850s, when several species (including red ironbark) were imported from Australia and planted as a potential source of timber and fiber.
The most prolific species in California (and in the world) is the fast-growing blue gum eucalyptus (Eucalyptus globulus), recognizable by its peeling bark layers and fragrant, oily blue-green leaves. Ironically, its wood turned out not to be an ideal timber for construction.
Red ironbark, by contrast, exhibits different properties. Its bark is thick, tough and highly furrowed, while beneath it, the red wood is strong, hard and dense. As timber, the durable wood has been used for beams, railroad ties and other construction projects. The tree is also drought- and frost-tolerant, which has allowed it to survive in non-native habitats.
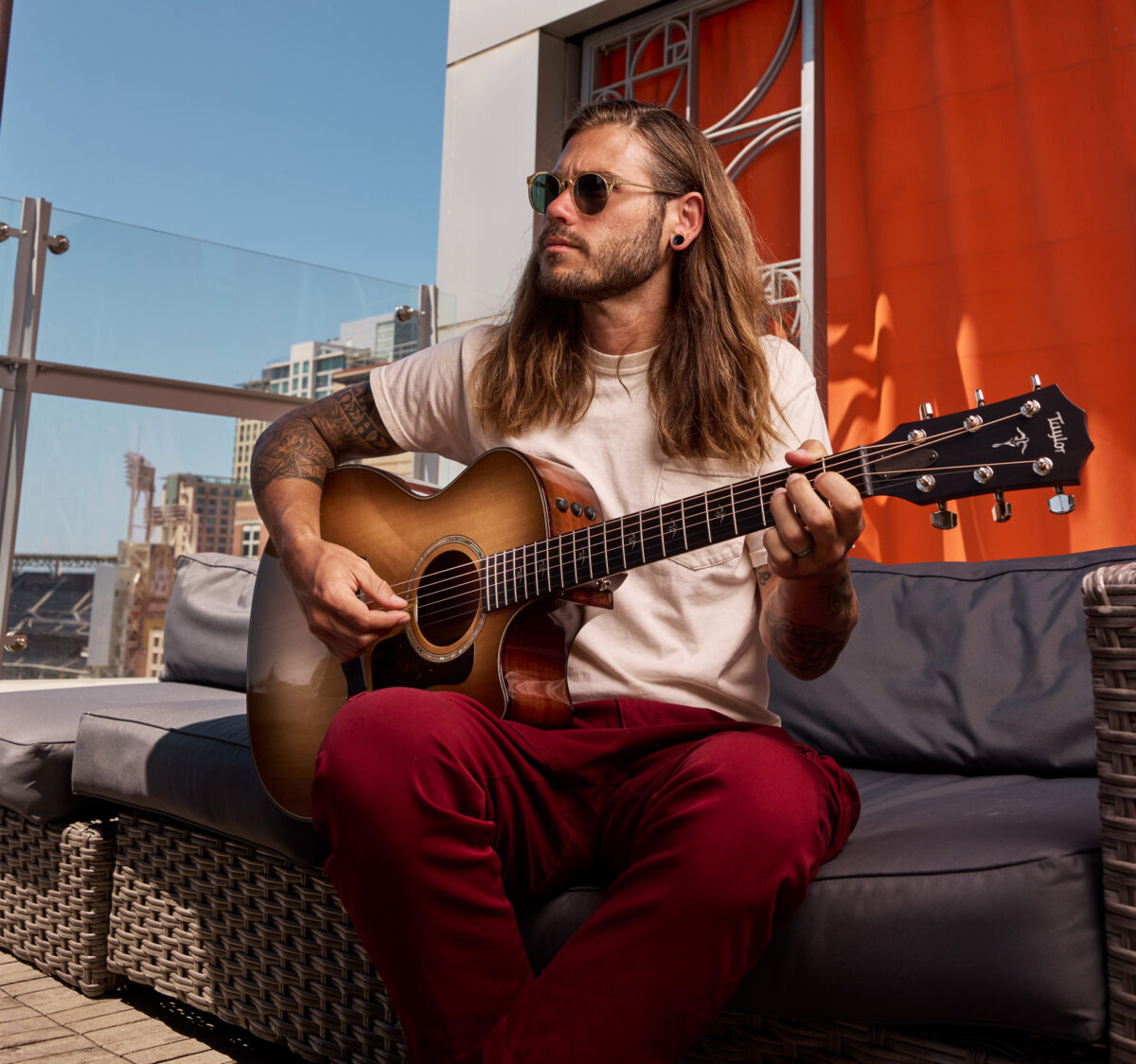
Shaping the Sound
Now familiar with ironbark’s structural properties, Andy developed a voicing recipe for a Grand Auditorium guitar and built some prototype models. As the top wood, he opted for torrefied (roasted) Sitka spruce. The two woods together, and voiced with a version of his V-Class bracing, amount to what he describes as a fresh variation on the classic spruce/rosewood sound — a cross between rosewood and ebony, he says — with the help of some modern acoustic engineering under the hood.
“The voice is bold, rich and sweet…it has a very piano-like character.”
—Andy Powers
“The red ironbark has a tone-shaping quality where it produces the deep, clear sound of rosewood but with just enough of the damping effect of ebony or mahogany that helps smooth out the sharp edges of the sound,” he says. “The voice is bold, rich and sweet. It has that bell-like amplifying response of a dense wood — it’s vibrant and dynamic. Imagine if you could take the traditional sound of a rosewood guitar, while filling and warming the midrange. It has a very piano-like character.”
In a demo session on the Taylor campus in June, Andy played the final version of his Grand Auditorium, and the first impression for those of us in the room is how much volume and projection the guitar produces, even with a lighter playing touch.
“It’s a high-fidelity sound that’s balanced by this sonic sweetness that makes a really appealing sound,” he elaborates. “When I strike that low note, it’s clear as a bell, and there’s nothing harsh about it. It’s not muddy; it’s not a spongy- or squishy-sounding wood at all. With the ironbark’s density, the guitar sound is what I would describe as muscular and strong. The sensation I get when I play it is like the guitar is amplifying everything I do. It’s giving me back more than I put into it — like the notes want to jump out of the guitar. These are guitars I’m really excited to get into people’s hands.”
Designing the New 500 Series
Having had ironbark prototype guitars around his studio for several years now, Andy has had a lot of time to think about how it might fit into our guitar lineup. And with more mahogany models being offered in the 300 Series, the 500 Series felt like an appropriate position to introduce these guitars. As the second urban wood featured in our line, it also marks another phase of our commitment to urban wood by showcasing it in a Taylor legacy series — one that has been around nearly as long as our iconic 800 Series.
To honor the classic heritage of the 500 Series, Andy embraced a traditional aesthetic but with distinctive decorative touches to complement the new wood pairing. The ironbark back and sides feature a subtle edge stain that deepens the wood’s natural reddish and golden-brown hues, resembling the colors of the mahogany it replaces. The body and neck also feature a lightly shaded edgeburst — the top’s subtle dusting of color adds an understated vintage look over the lightly darkened roasted spruce top. The body features gloss finish and satin finish for the neck. Other appointment details include an elegant new “Aerial” inlay scheme in Italian acrylic, with a faux tortoise shell pickguard and binding, a single-ring abalone rosette with maple and black purfling, and Taylor nickel tuners.
In terms of model offerings, we’re launching the revamped series initially with just two body styles — the Grand Auditorium 514ce and Grand Concert 512ce — with other models likely in 2023. (One side note: The existing Builder’s Edition 517 will remain the same, retaining its mahogany/torrefied spruce wood pairing and other appointments.)
If anything, the volume and richness of the sound may be even more impressive coming from the Grand Concert edition, given the smaller body. Andy played it in his demo session, and the tonal output was remarkable.
“It’s clear, clean and pretty, but with surprising volume and that piano-like richness,” he says. “Even though it’s a Grand Concert, I could start strumming chords [he does], and it really delivers. I’m thrilled with how it’s working.”
For more reactions to our new 500 Series guitars, see our roundup of artist feedback.
Meet the New 500 Series
514ce
Our first Grand Auditorium guitar featuring back and sides of Urban Ironbark, the 514ce delivers a sweet, muscular sound that combines rosewood’s high-fidelity voice with mahogany’s warm and punchy midrange and spectrum-wide sonic balance. Paired with a torrefied Sitka spruce top for a played-in, mature sound and V-Class bracing for improved volume and sustain, the 514ce yields power ideal for heavy strummers along with touch sensitivity that gives it a wide dynamic range that’s great for fingerstyle players. With new Aerial inlays in Italian acrylic, a single-ring abalone rosette, a subtle stain that highlights Urban Ironbark’s rich red hues, a lightly shaded edgeburst and gloss-finish body, the 514ce blends traditional and contemporary visual styles.
512ce
The 512ce is one of our first models to feature back and sides of solid Urban Ironbark, a dense, hard tonewood that yields a rich, sophisticated response with a deep low end and high-fidelity voice reminiscent of Indian rosewood, along with some of mahogany’s midrange punch and focus. The Grand Concert 512ce pairs Urban Ironbark with a torrefied Sitka spruce top, lending a played-in character that makes for a warm, piano-like sound with remarkable balance across the tonal spectrum. With V-Class bracing inside, this compact acoustic-electric serves up room-filling projection and blooming sustain, offering a muscular quality that remains sensitive to a soft touch. Appointments include new Aerial inlays in Italian acrylic, a single-ring abalone rosette trimmed with maple and black purfling, and a tastefully subtle edgeburst.